Our industrial maintenance services
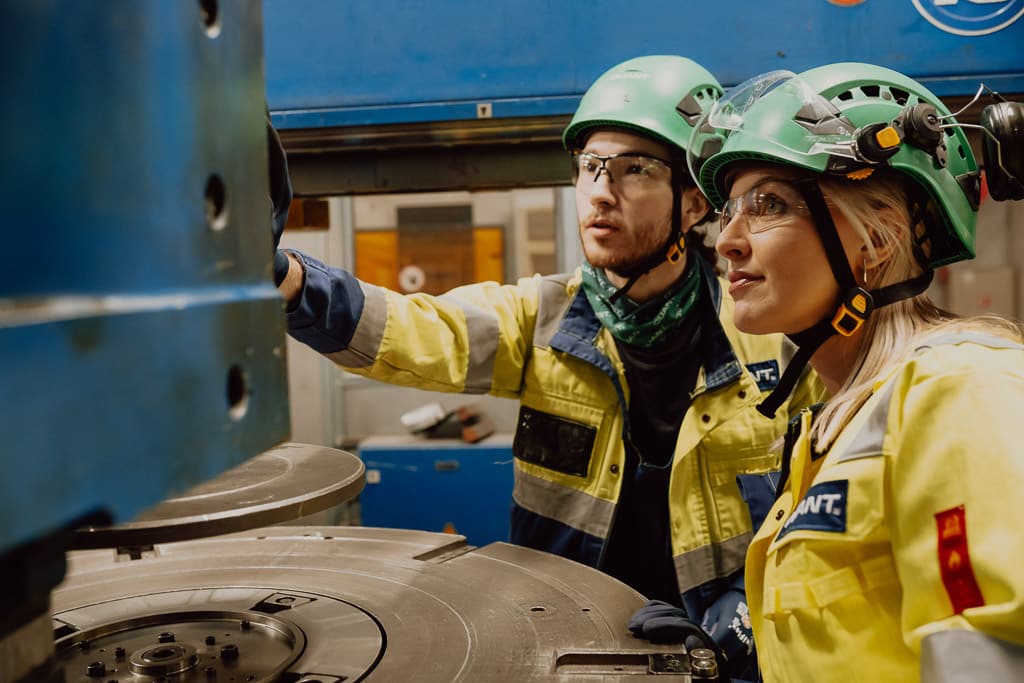
Looking for unique solutions
in industrial maintenance?
Quant is a leader in the global industrial maintenance services market, working in almost every industry. Quant’s services are offered through tailored partnerships emphasizing shared risk and return, common objectives, and business benefits linked to each unique customer situation.

Our core
offering
Our partnerships are tailored to suit each unique customer situation. We have partnerships for greenfield projects, maintenance execution, or when you want a partner taking full responsibility for all aspects of maintenance.
In addition, we offer tailored partnership services such as asset and maintenance management, engineering and project services, shutdown management, etc.

When to partner
with Quant
Whether you need a maintenance partner for a greenfield project, when in need to transform and optimize your maintenance operations, or when maintenance is not your core business, Quant is your choice.
We provide support in all stages; when establishing, transforming and maintaining maintenance operations.
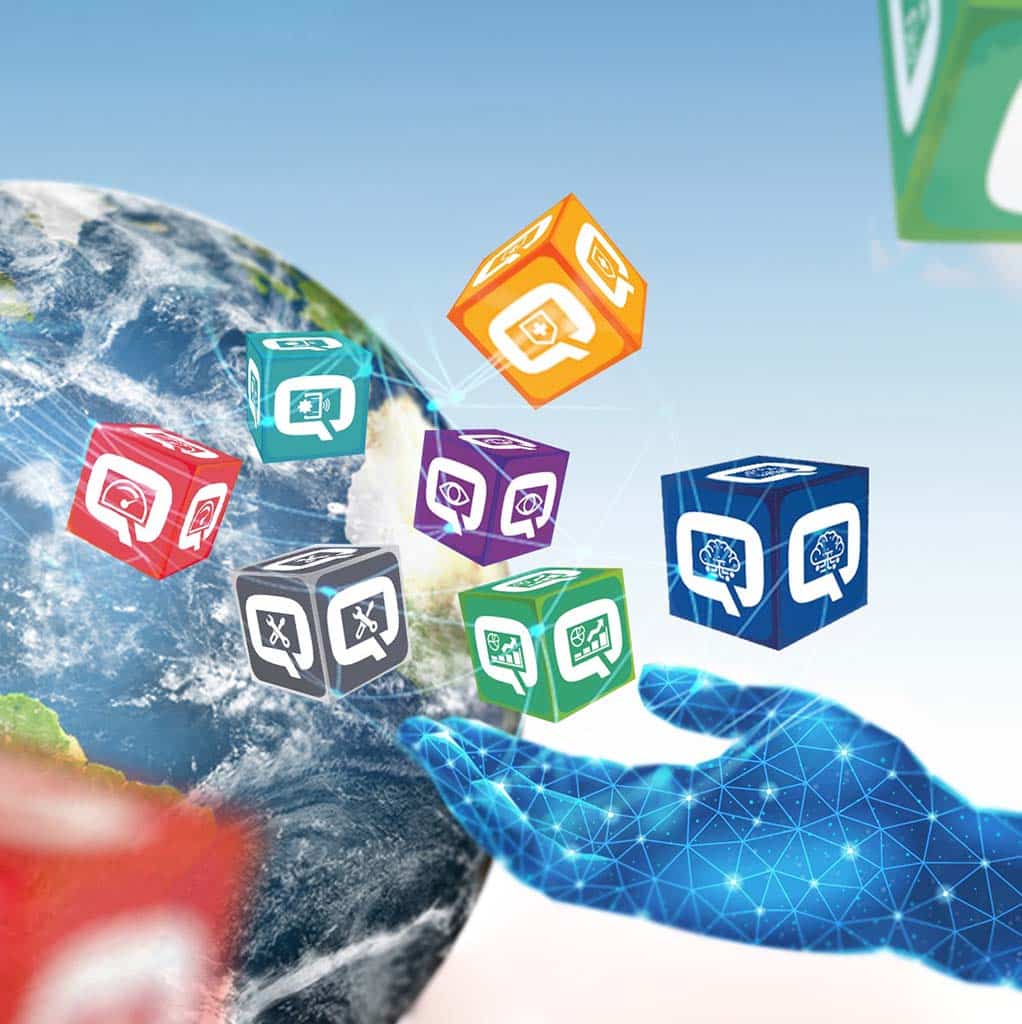
Quant Smart Maintenance
The core of our value proposition consists of improving safety, creating organizational equity, driving plant performance, and cost alignment. The approach is to view the maintenance function as a profit contributor, and not as a cost center, with Quant as the partner driving this transformation.
By partnering with Quant, we support you on your journey towards Smart Maintenance.

Benchmark and improve your maintenance performance
We have gathered extensive maintenance insights for over 35 years, through some 1,000 feasibility studies performed worldwide. Predominantly in pulp & paper, discrete manufacturing, metals and mining, oil & gas and food & beverage. Are you interested in benchmarking your maintenance performance with peers in your industry?
Please provide a few details about your current maintenance situation and we will provide a high-level benchmark free of charge. If you preferer, we will contact you to for an online consultation on how you could improve your maintenance operations.
Some industries we work in
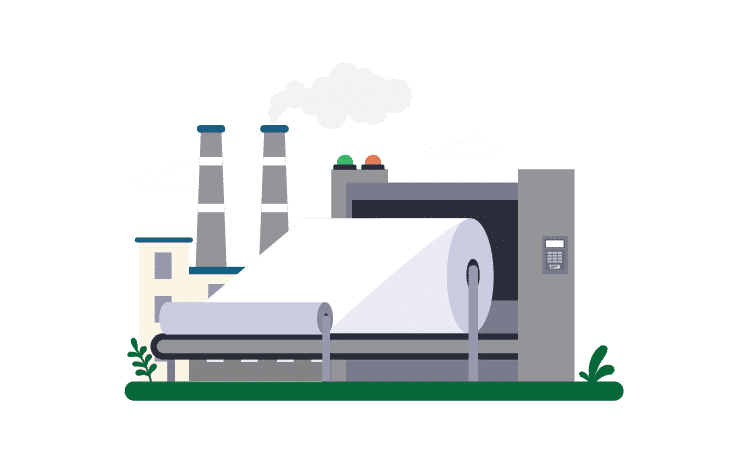
Pulp & paper
Are you interested to learn more about what we have done for our customers working in pulp & paper? We have extensive experience from partnering with companies in this industry, please reach out and we are happy to discuss how we can support you!
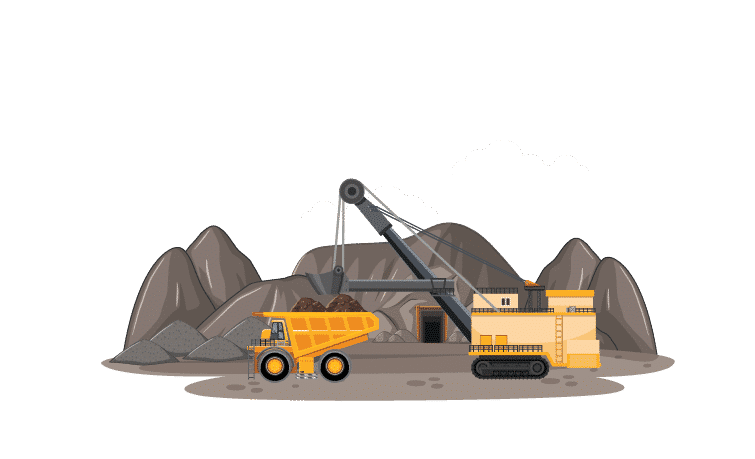
Mining & minerals
The customer, an international blue-chip company in the mining industry and owner of several mines worldwide, needed to achieve a competitive cost per ton copper produced entailing improved efficiency in its full value chain.
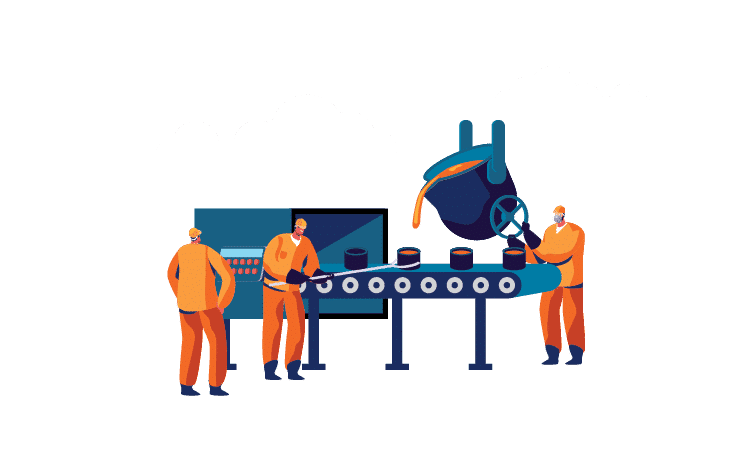
Metals
Are you interested to learn more about what we have done for our customers working in the metal industry? We have extensive experience from partnering with metal companies, please reach out and we are happy to discuss how we can support you!
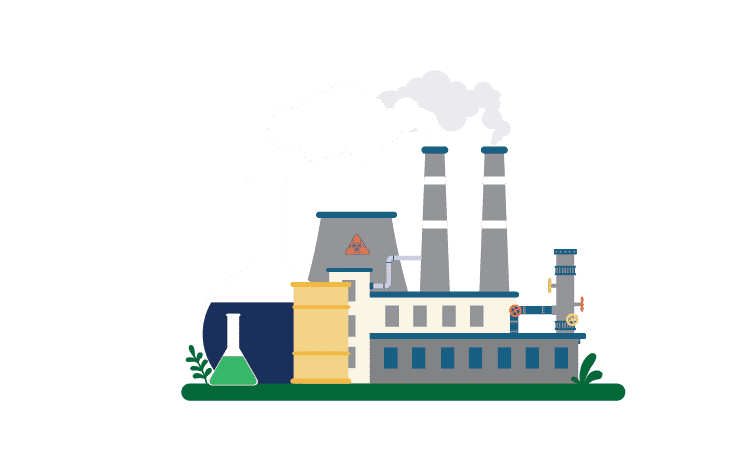
Chemicals & petrochemicals
The customer, a worldwide industrial and automotive lubricant oil and grease producer, partnered with Quant with the targets to achieve zero accidents, improved technical availability for filling and grease production lines, and reduced overall plant production costs.
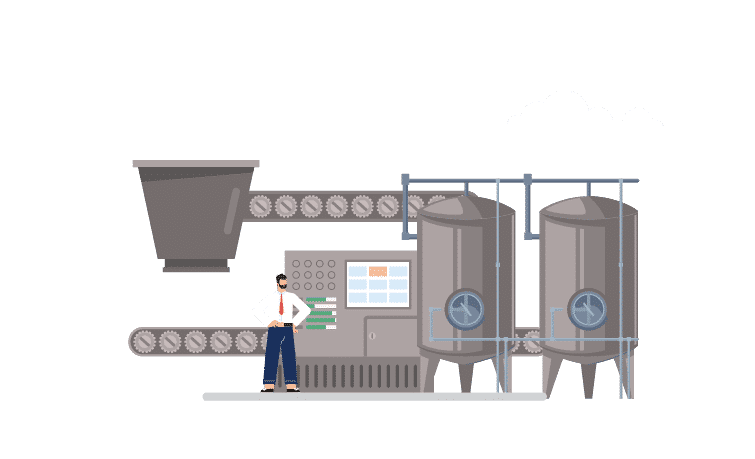
Food & beverages
The customer, a food & beverage incumbent owning a chain of industrial bakeries in the Nordic region, needed to professionalize maintenance operations to increase the productivity in one of its bakeries.

Discrete manufacturing
The customer, a producer of power distribution solutions with five major industrial plants in Europe, needed to improve maintenance operations to support the transformation to world leading operations, with ambition to improve output as well as cost ratios for all its plants.
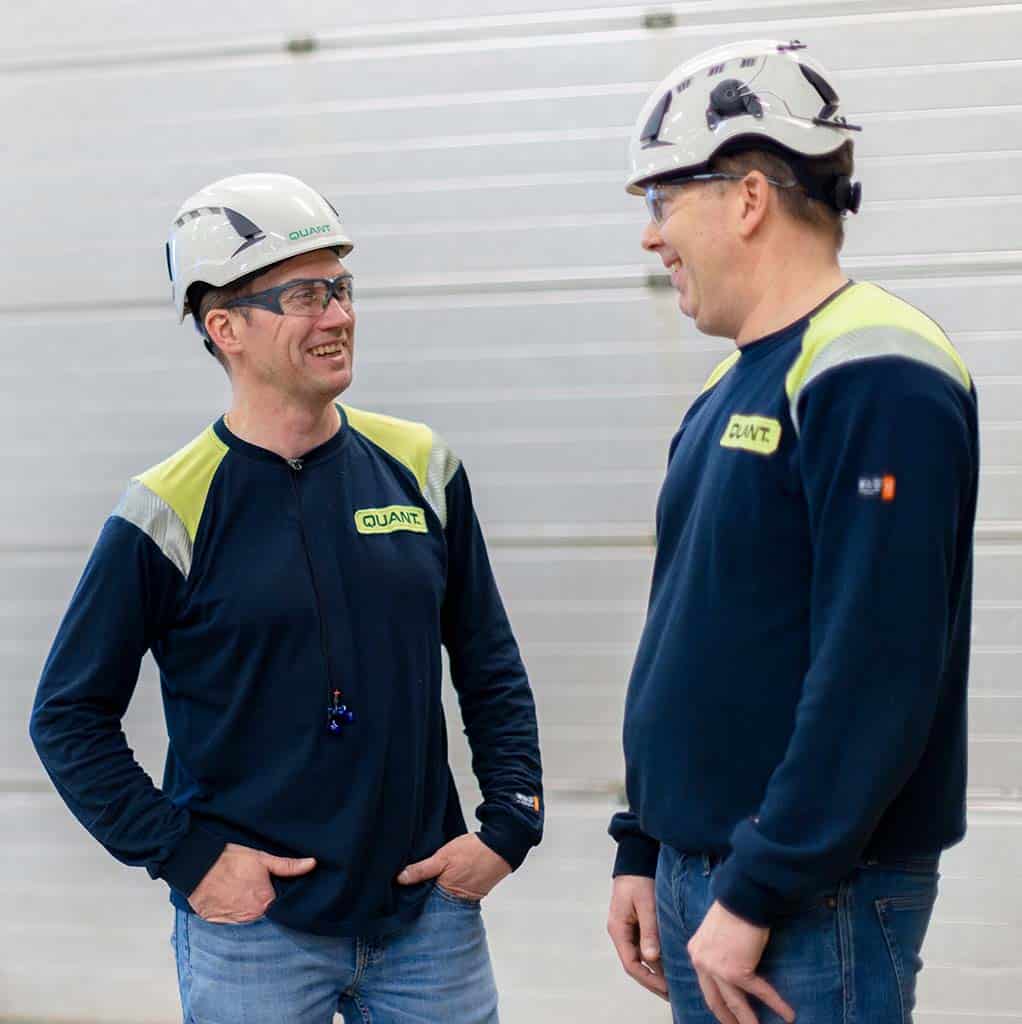
Safety and sustainability
at the center of operations
We are committed to manage our business and deliver our asset and maintenance services in a sustainable way, preventing harm to employees, customers, contractors, local communities, and the environment. Our aim is zero incidents, and to become and remain the best in class.
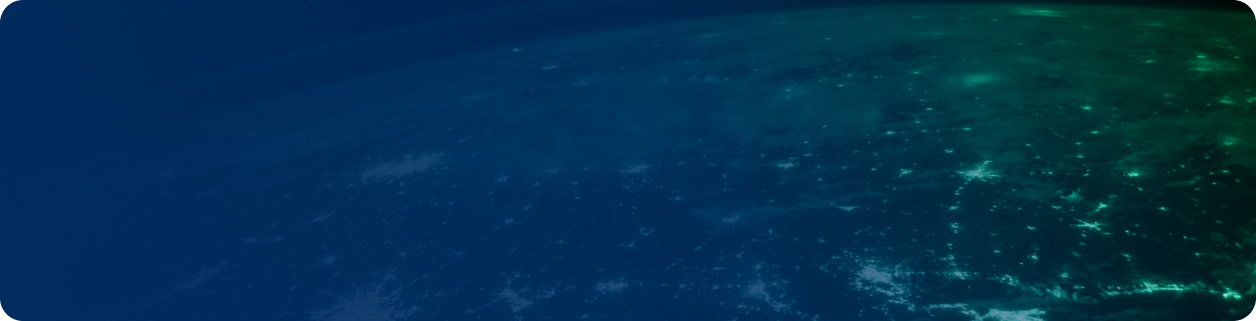
Curious about what
we can do for you?
With our wide network and solid experience, we can support customers in a wide range of industries and locations.
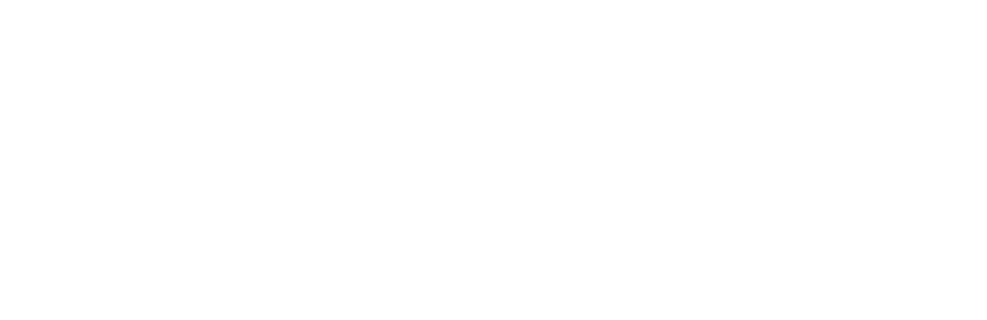