November 27, 2024
Predictive maintenance – Collaboration between people and data leads to results
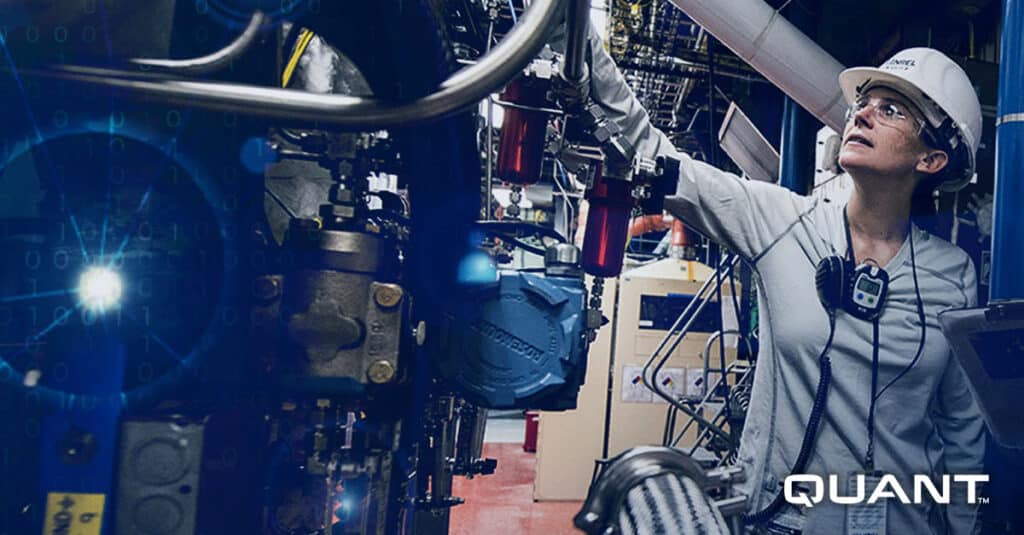
Effective maintenance is at the heart of success in factories and production plants. Ensuring that the production runs smoothly and results in maximized output requires an understanding of how to prevent problems. In turn, understanding requires fact-based information about the operations of production equipment and lines.
If a manufacturing facility focuses solely on ensuring that if something would break, spare parts and repairmen will ready, then every equipment failure interrupts the production and is unexpected in nature, which often leads to additional costs. In these situations, technical availability is often based more on luck than skill.
Nowadays, more and more companies are using various systems to monitor equipment utilization, which collect data for equipment operations and the causes of outages. By actively monitoring and analyzing this data, deviations can be identified, and corrective measures can be taken. This allows maintenance to be planned and enables a shift towards predictive maintenance, where maintenance is performed before a failure occurs.
Utilizing real-time data
Without real data and OEE measurement, it is difficult to find a clear reason to why production stops, if it does. Conversely, without data, we cannot know what changes have contributed to keeping production running. Therefore, data plays a key role.
With systematic preventive maintenance and collected data, Quant can identify problem areas and take the necessary measures before production is interrupted. That is why the cornerstones of predictive maintenance are regular inspections, data analysis, and continuous improvement.
When maintenance is planned and data-driven, we can accurately predict maintenance needs. This improves production flow, reduces unexpected production downtime, and improves cost management. We can also reduce the need for urgent purchases. When the basic pillars of predictive maintenance are in place and proactive measures are actively implemented, the indicators often show a clear change for the better. This means more production for the production plant.
The importance of human competence
Data is an important tool, but it does not replace human expertise and systematic operating models. Maintenance professionals with long experience know the equipment best and can detect problems that the data may not reveal. When we combine data analysis and the expertise of experienced professionals with planned maintenance execution, they form an effective whole.
Lauri Kaiharju
Sales manager, Quant Finland