January 30, 2025
Modern technology and maintenance analytics drive production growth
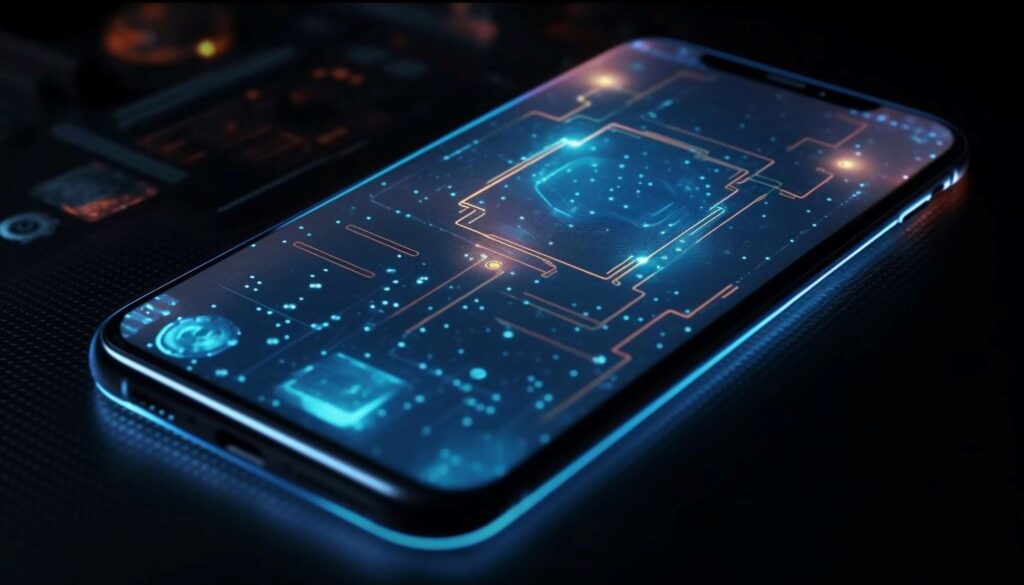
In an era where technological advancements are reshaping industries, the integration of cutting-edge tools and analytics has become a cornerstone for achieving operational excellence. From manufacturing to energy sectors, the adoption of IoT sensors, Artificial Intelligence (AI), Machine Learning (ML), and data analysis is revolutionizing maintenance operations. These technologies not only prevent downtime and extend equipment life cycles but also reduce costs, enhance product quality, and boost overall efficiency. As industries strive to stay competitive, the role of these innovations in driving production growth and promoting sustainability cannot be overstated.
Robert Berkel, Head of Digitalization & IT at Quant, has been implementing modern solutions to streamline industrial maintenance processes. “Typically, maintenance strategies have been reactive, meaning maintenance personnel react to equipment failures that have already occurred. Our goal is to leverage technology-enabled tools such as IoT sensors and AI to foresee and prevent potential equipment failures,” says Berkel.
By developing a maintenance strategy and utilizing modern technology, it is possible to improve the production efficiency of a facility by up to 30%, depending on the initial situation and industry field. “We implemented a project at our customer site, installing IoT sensors on the most critical devices based on criticality classification results and connecting them to a cloud-based system. We managed to reduce unplanned down time by 144 hours, on just one plant” Berkel says.
IoT Sensors and Machine Learning Increase Production Efficiency and Reduce Costs
IoT sensors collect device-specific data about the condition, operating conditions, and performance of the machine into the maintenance system, which can be analyzed to implement predictive maintenance measures. Typically, IoT sensors measure temperature changes, vibration changes, pressure differences, humidity changes, or changes in power consumption.
“Machine Learning, a branch of artificial intelligence, is based on algorithms. It has revolutionized industrial maintenance over the past few decades. Advanced machine learning algorithms predict potential equipment failures from collected data, helping the maintenance organization schedule proactive maintenance, minimize production downtime, and optimize resource utilization,” says Berkel.
The greatest benefits of using modern technology to improve maintenance efficiency are typically obtained in fields where production interruptions cause exceptionally high costs, such as manufacturing and energy.
With the information obtained through digital solutions, the maintenance organization plans maintenance for the equipment using data analysis and information created by artificial intelligence. Early-stage maintenance significantly impacts the device’s service life, allowing for substantial cost savings and better scheduling of future investment needs.
Data Analysis and Visualization Make Decision-Making Faster
Typical uses for visualization panels include monitoring equipment health, optimizing production processes, monitoring energy consumption, and managing inventory. For example, a visualization panel can display real-time metrics, trend charts, or histograms.
Real-time information that is available and easy to read improves and speeds up decision-making. Predictability helps minimize production downtime and extends the life cycle of equipment, as equipment can be serviced before it fails, which is often more cost-effective. By optimizing production processes, it is possible to increase production and reduce waste.
Sustainability Through Technology
In addition to operational benefits, the integration of modern technology in maintenance practices significantly contributes to sustainability efforts. Predictive maintenance reduces the need for frequent replacements and repairs, thereby minimizing waste and conserving resources. Energy-efficient operations, enabled by real-time monitoring and data analysis, help lower the carbon footprint of industrial activities. By extending the life cycle of equipment and optimizing resource utilization, these technologies support sustainable production practices and contribute to a greener future.
Enhancing Safety Through Predictive Maintenance
The integration of modern technology in maintenance practices not only boosts operational efficiency but also significantly enhances workplace safety. By utilizing IoT sensors and machine learning algorithms, potential equipment failures can be predicted and addressed before they occur. This proactive approach minimizes the risk of accidents and injuries caused by unexpected equipment breakdowns. Additionally, real-time monitoring and data analysis enable maintenance teams to identify and mitigate safety hazards promptly, ensuring a safer working environment for all employees. The adoption of these advanced technologies underscores our commitment to maintaining the highest safety standards while optimizing production processes.