September 5, 2023
Saving production downtime and improving equipment availability
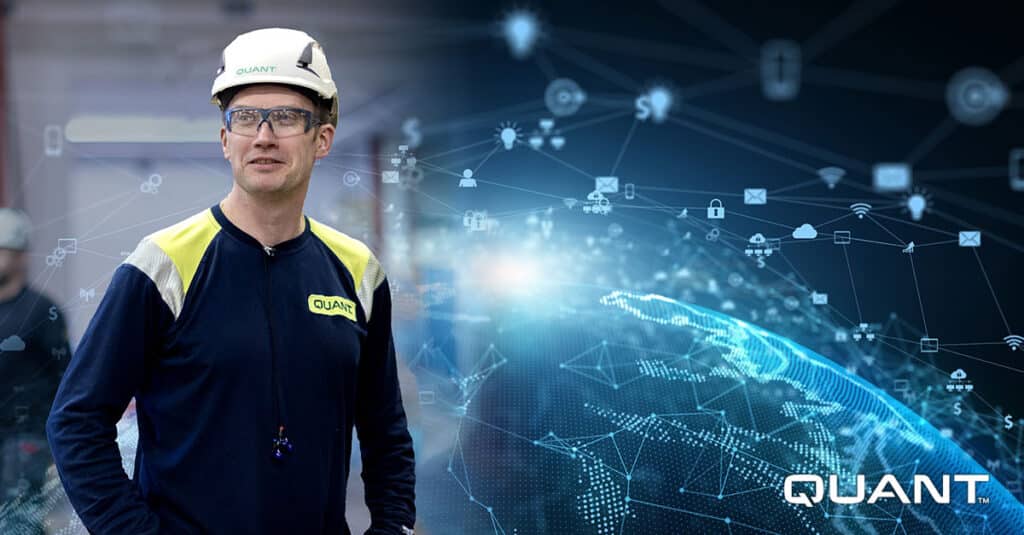
At our site in Louisville, Kentucky, we have an ongoing project together with our customer to install temperature sensors on all assets. This allows us to shift towards a predictive maintenance approach, minimizing downtime and making work safer.
– We run about under one percent downtime, so most of our equipment availability is 99 percent, if not 100, says Quant Site Manager Alan Ricchio.
Our contract with the appliance manufacturer based in Louisville, Kentucky, started in 2017. The scope of work includes preventive and corrective maintenance of production equipment, facility, and vehicles, as well as repairing finished goods. In 2020, we started a condition monitoring project together with the customer to install temperature sensors on all gearboxes in the critical production path to prevent failures and enable a condition-based maintenance approach. When the project is completed, we will have installed more than 400 sensors.
Saving production downtime
The sensor for each gearbox is programmed with upper and lower limits for the normal operating temperature range. Any temperature sensed outside of this window indicates an abnormal condition and generates an alert.
– This enables us to schedule the repair when the plant is not running. We have over 400 pieces of equipment so having these sensors helps us detect potential failures easier, saving downtime for the production, says Quant Site Manager Alan Ricchio.
Installing sensors has also made the maintenance work safer.
– When you do not have to do emergency breakdown repairs, it is always safer. You have more time to do your risk assessment and plan the repair instead of being rushed, Alan says.
– In an environment such as the mining industry, these temperature sensors would be even more valuable. It would be great in a chemical or toxic environment, but fortunately we do not have that here.
High equipment availability using sensors
The visual graphic of the monitoring system gives a clear overview of all assets in real time, allowing quick response to breakdowns, leading to a high level of equipment availability.
– We run about under one percent downtime, so most of our equipment availability is 99 percent, if not 100. The sensors enable us to monitor the assets in real time all the time, and that allows us to respond very quickly to breakdowns.
When all sensors are installed, the next step of digitalizing the maintenance operations even further could be to install cameras that scan all products and alerts if there are any deviations.
– It is great that we have the resources and technology to be able to offer these kinds of solutions to our customers. It makes us more responsive and proactive, being able to shift towards a condition-based, predictive maintenance approach, Alan says.