July 1, 2025
5 ways to manage maintenance risks – a critical factor for competitiveness
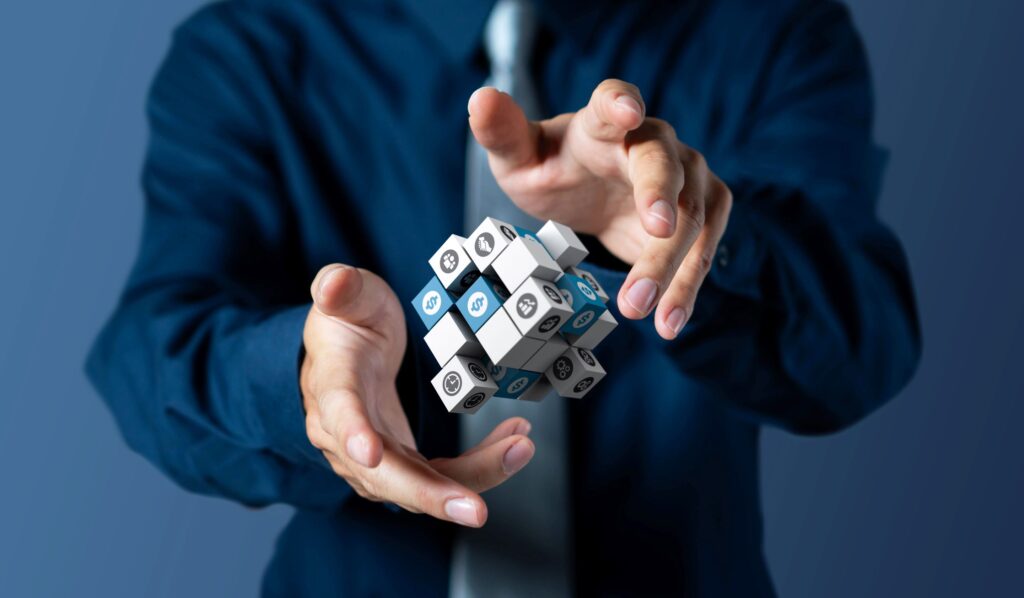
In an industrial environment, maintenance risk management is not just a support function, it is a core part of production and business management. When maintenance fails, the impact is immediate: unplanned downtime, production disruptions, customer dissatisfaction, and uncontrolled costs erode performance and challenge competitiveness.
The good news? Maintenance risks can be systematically managed. With the right data, clear responsibilities, and consistent processes, maintenance shifts from reactive firefighting to a proactive, business-supporting function. Here are five perspectives to help you secure maintenance continuity, production reliability, and, above all, turn risks into manageable factors.
1. Make criticality visible – focus maintenance where it matters most
Effective resource use in maintenance starts with understanding which equipment and systems are critical to your business. By clearly defining criticality for both production and spare parts, maintenance can be systematically managed, targeting actions where the risks are highest and the impact on production is most significant.
Criticality analysis ensures preventive measures, spare parts management, and resources are directed to the right targets. The result is improved production continuity, reduced downtime risk, and a controlled maintenance cost structure.
Read more: Criticality analysis for optimizing maintenance and spare part strategies
2. Maintenance brings solutions to the table – not just reports problems
A single failure does not resolve anything; what matters is how it is addressed. Maintenance creates value not by simply reporting disruptions but by providing clear actions and improvements that keep production running.
When maintenance communicates proactively and clearly, it supports decision-making across the organization and enables anticipation. This builds trust, enhances collaboration, and directs resources to the right areas. Data-driven maintenance starts with interpreting failures correctly and responding to them systematically and effectively.
Read more: Predictive maintenance – Collaboration between people and data leads to results
3. Predict, don’t react – let data guide timely maintenance actions
Time-based maintenance leaves too much to chance. Instead, data-driven predictive maintenance enables actions when they are truly needed, not too early, not too late.
By using condition monitoring, real-time system data, and analytics, maintenance evolves from a reactive approach to a proactive process. This extends equipment life, reduces downtime risk, and improves overall production performance.
Predictive maintenance is not just a technical solution; it is a strategic choice that strengthens competitiveness and supports business continuity.
Read more: Modern technology and maintenance analytics drive production growth
4. Clear responsibilities and processes build reliability
Maintenance should never rely on assumptions. Unclear responsibilities, boundaries, and processes increase the risk of errors and threaten production continuity. When maintenance roles, metrics, and ways of working are clearly defined, operations become controlled, efficient, and transparent. This applies to both internal teams and outsourced maintenance.
A well-structured operational model provides security, ensuring the right actions happen at the right time, even during high-pressure situations.
5. The right partner supports where production needs it most
In an industrial environment, maintenance becomes even more critical when production targets tighten and resources must be used efficiently. An experienced maintenance partner brings process expertise, the right tools, and proven operational models. When the collaboration is grounded in a true understanding of your business, maintenance becomes a strategic asset rather than just a cost.
A strong partnership ensures that risks are not just reacted to they are anticipated, managed, and eliminated together in support of production goals.
Read more: Is your maintenance efficiency fully realized?
Maintenance risks are manageable when you see the big picture
Maintenance risk management is not a single action; it is an integral part of holistic production management. With accurate data, effective systems, clear roles, and a committed partner, maintenance shifts from reactive to proactive and becomes a true business enabler.
In practice, this means higher equipment availability, better production quality, and the agility to respond to changes swiftly and effectively. Well-managed maintenance is not just about controlling costs; it is an investment in production continuity, safety, and long-term competitiveness.