May 14, 2024
Quant & Heidelberg Materials Kunda AS – replacement of cement mill body
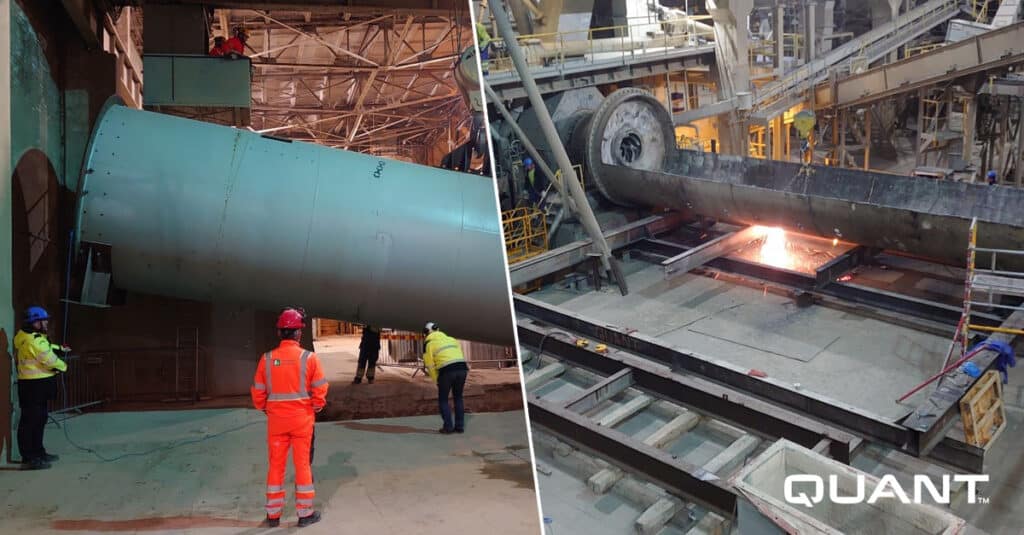
Our long-time customer Heidelberg Cement Kunda needed support in the renovation project of an old cement factory in Estonia. Our customer had faced challenges in replacing the body of the fourth cement mill, which measured 3×14 meters and weighed 40 tons.
On average, the life cycle of a cement mill body is usually around 40-50 years. The customer’s approximately 40-year-old cement mill body showed clear signs of wear and had cracks which had been welded over the years. However, now the body of the cement mill was considered to be at the end of its life cycle, and it was found that a renewal was necessary.
– As our client’s long-term maintenance partner, we offered a solution to their challenge, and they trusted our team’s previous experience of similar projects. We started the project together and coordinated the necessary changes along the way, which needed to be made in the starting phase of the work and included in the planning, in accordance with the needs of the production, says Taavi Saart, Project Manager, Quant Estonia.
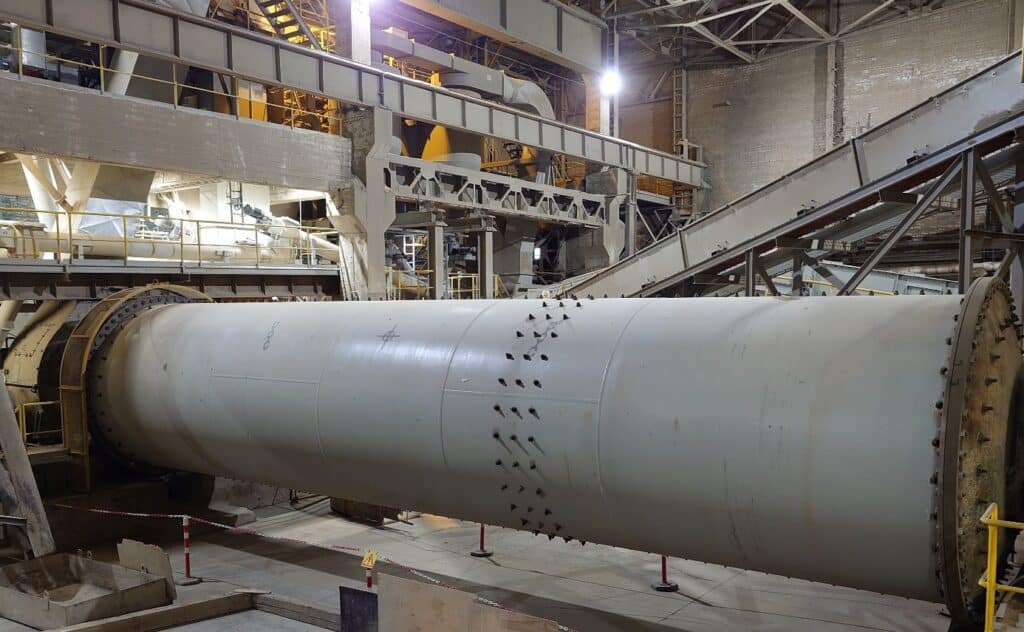
Project started with disassembly work
Our local team decided to use a technology similar to the one previously used in a project a couple of years ago.
– The cement mill project started with the removal of the old body’s lining plates and intermediate diaphragm. We also braced the mill heads and drive shaft. At the same time as we were cutting the old frame into smaller pieces, we were building a steel beam frame in the production space to accommodate the new body. The success of the project sometimes also required creative thinking, says Taavi.
Transporting the new body into place inside the building was time critical.
– In certain work phases, we had to dismantle equipment from other production lines, which had to be put back into operation within two-three days. After replacing the cement mill body, it is particularly important to align the mill’s body and the drive, which required the assistance of a surveyor, Taavi says.
Once the body was in place, the work continued with the installation of new lining plates and intermediate diaphragm. The smooth cooperation between Quant and our customer ensured a successful project and its completion according to schedule.
– The customer was satisfied with our work and the most important thing was that the mill was aligned, and we stayed within the predetermined timeframe. The client appreciated our professional approach and previous experience. Big thanks to our amazing team who helped make this project a success!
This is a good example of a project where production line renewal, big heavy parts, hauling, assembly and disassembly were completed successfully under a tight schedule while fulfilling the needs from the production.