November 7, 2024
Less production downtime and improved safety with predictive maintenance
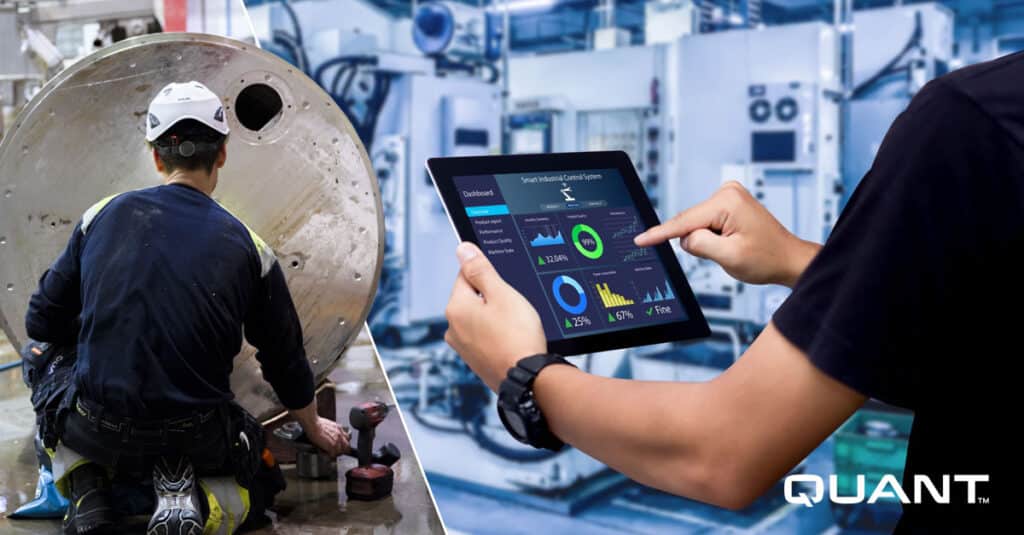
At our site in Baden, Switzerland, we are running a technical evaluation piloting a new type of service together with our partner IPercept. This digitalization initiative is enabling a predictive maintenance approach based on the equipment’s condition by foreseeing where potential failures could happen. Early results show a reduction in production downtime and improved ability to better plan the maintenance work. This also adds the benefit of allowing more time for a comprehensive risk analysis of the planned work.
Together with IPercept, a leader in industrial software solutions specialized in predictive maintenance and machine operational improvement solutions, Quant Switzerland has been running a technical evaluation to implement smart IIOT devices on key equipment in the operations.
For our site in Baden, IPercept have supplied smart IIOT devices which have been installed, enabling a shift towards a preventive maintenance approach. With less downtime and a larger portion of planned maintenance work, we have seen great results which have also been recognized by our customer.
– This technical evaluation has been successful. It demonstrates how we can support our customer, significantly improving operations in a short period of time, says Oliver Harnisch, Quant Site Manager in Baden.
Identifying a potential failure
Cloud-connected smart IIOT devices measuring different factors such as ultra-high sensitivity motion have been installed in key machines of the production. The data is collected in the cloud and run through analysis algorithms. This produces a health score for various points of the equipment which are compared over time, and we can from this data see the degradation of the equipment over time and thus plan for the necessary maintenance in advance. This allows the team to ensure the correct spare parts are in place ahead of starting the work, which reduces the risk of prolonging the maintenance.
With the detailed level of information provided by IPercept, specifying the location and the exact component in the equipment where the failure is originating, the risk for the technician performing the maintenance work is further reduced and their focus can be on the correct location in the machine.
Improved risk detection and injury prevention
Another key benefit is that the safety in connection with maintaining the equipment is further improved.
– When the team can plan their work well in advance, it leaves even more time to do a comprehensive risk analysis to identify potential risks. This makes working conditions even safer, minimizing time pressure, allowing us to do mitigating actions well in advance to ensure the safe execution of the maintenance, Oliver says.
Having a comprehensive risk analysis done and potential hazards identified allow us to have a plan in place to ensure the safe completion of the maintenance. For example, the correct personal protective equipment to prevent hand injuries, which are the most common type of injury, can be procured and used during the maintenance work.
– Since we already know where the potential failure is, we must only check a certain part of the machine. This decreases exposure to heavy lifting, sharp objects, hanging components, and several other risk factors associated with our work, Oliver says.
Robert Berkel, Digital Product Area Manager:
– This is an exciting new capability we can add to our digital toolbox, improving the way we can monitor our customers’ equipment, allowing us to focus on the correct equipment. This will increase the technical availability and allow us to better plan the work to make it even safer and more efficient, and we are looking forward to starting up more projects with this capability.