March 21, 2024
Greenfield cases: “Attention to maintenance is often drawn too late”
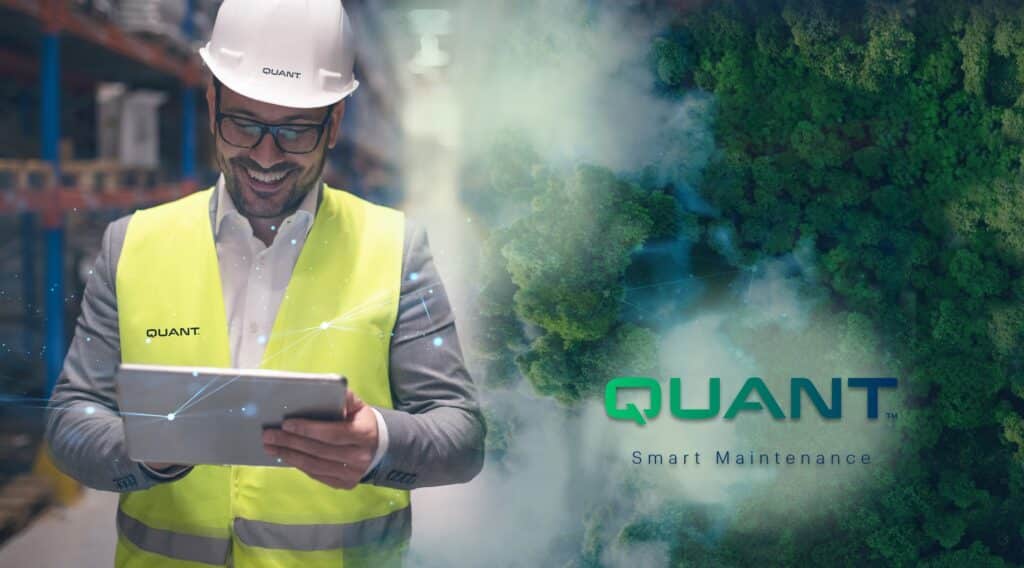
In the profitability analysis of a new greenfield factory project, the aim is to analyze and take into account several different perspectives and scenarios. Key factors in the profitability analysis include investment and financing costs, operating expenses of the facility, production volume and utilization rate, demand for products and selling price, investment payback period, as well as environmental impacts, risks, and uncertainties.
Typically, maintenance is evaluated as part of the factory’s operating expenses, specifically as a cost element. However, maintenance is a function that impacts several key factors. Maintenance related decisions can significantly affect the operating costs, lifecycle, and even the investment payback of a production facility, as well as its profitability. Recognizing the importance of maintenance early in the project development phase is thus crucial.
Attention to maintenance is drawn too late
It is natural and inevitable that after the investment decision of a new factory, focus and the greatest efforts are directed towards plant design and, ultimately, construction. The primary objective of a massive project is to get the factory‘s walls up, the roof on, and the equipment installed once construction begins. Often, maintenance is considered much later in the construction phase.
This situation is quite understandable when considering where attention is typically focused in factory projects; designers are tasked with producing feasible plans and solutions according to specified requirements, equipment suppliers focus on providing the necessary technology for production, construction and installation contractors focus on their respective tasks, and project management oversees all of this. No wonder then that individuals lack the time or necessary expertise to consider factory maintenance and reliability at this stage!
However, at Quant, we see things differently. It is of paramount importance to recognize that the completion of the factory project itself is not the primary objective, but rather the efficient, safe, and sustainable production of the facility. When the facility is handed over to end users, maintenance processes, resources, and tools must be ready to support a smooth production ramp-up and the achievement of sustainable production levels as quickly as possible.
Save yourself from unwanted surprises
It has been said that up to 80% of the lifecycle costs of a production facility are determined before its commissioning. Therefore, it is extremely important to make the right choices and decisions in the design phase, considering the entire lifecycle of the facility.
The insights of maintenance professionals during the design phase can prevent many unpleasant surprises in various stages of the factory’s lifecycle; have equipment and component selections been harmonized and are lifecycle services available for them? What about the availability of spare parts – are the devices easy to operate and maintain? Maintenance professionals are capable of considering and providing consultation on these significant matters from the end-user’s perspective.
Three important cornerstones
The successful maintenance operation of a new factory, or indeed any factory, should be built on three important cornerstones:
First and foremost is a high-quality, well-structured, and sufficiently detailed equipment hierarchy and maintenance master data integrated into a performance-oriented maintenance system. A quality equipment hierarchy and master data are the most important factors for facility lifecycle management. They enable precise analysis, classification, and reporting of equipment failures, as well as maintaining coherent historical data. These, in turn, support initiatives such as data-driven reliability maintenance development and targeted action. They also have a significant impact on key metrics such as maintenance performance and maintenance costs.
The second cornerstone is the classification of equipment criticality. Often in new factory projects, a comprehensive criticality classification covering all production equipment may not have been developed. Instead, the most critical parts and components of a certain production line or equipment may be identified, or perhaps the criticality of a device or a line is assessed solely in relation to production. It is clear that developing a comprehensive criticality classification is complicated by the lack of historical maintenance data for new plants. Nevertheless, it is important to establish criticality classification to ensure that maintenance and spare part strategies can be defined as accurately as possible at the beginning of the factory’s lifecycle. Furthermore, equipment criticality classification may reveal items that, due to safety or environmental impacts caused by equipment failures, become critical, even if their impact on other aspects of criticality such as production, quality, and repair costs, is estimated to be minimal. Criticality classification can also help identify potential bottlenecks in advance, which could require costly and extensive changes immediately after the factory’s commissioning.
The third cornerstone is spare parts strategy, which today, due to the vulnerability of supply chains, plays perhaps an even more prominent role in ensuring the reliability of production facilities. It is very common that spare parts packages acquired in factory projects from equipment manufacturers contain not only necessary spare parts but also a lot of off-the-shelf items and parts that are never needed. These million-dollar boxes may end up unused for a long period of time until it is eventually realized that these expensive parts serve no purpose.
By paying attention to the spare parts strategy developed based on equipment criticality classification, the worst pitfalls can be avoided, such as excessive capital tied up in spare parts inventory, poor spare parts availability, and weak predictability of maintenance material and spare parts costs. When developing a spare parts strategy, it is important to consider various availability and exchange services, consignment stocks, and shelving services, as well as defining the essential parts to be self-stored. There are options available, and all choices should support the reliability of the facility.
A trusted maintenance partner
In addition to these key cornerstones, there are numerous other factors to consider, such as defining the maintenance operating model, user maintenance, systems, and organization, which should be contemplated well in advance at various stages of a greenfield project before the completion of the factory.
As described above, considering these matters in the midst of a project, with the goal of completing the factory’s walls, roof, and equipment installations, may be overshadowed by other priorities. This should not be the case, and at Quant, we are ready to take the bull by the horns to support the success of new greenfield projects.
Mikko Haanpää
Development Manager, Quant Finland