February 13, 2025
Ensure effective processes for analyzing and managing spare parts warehouse
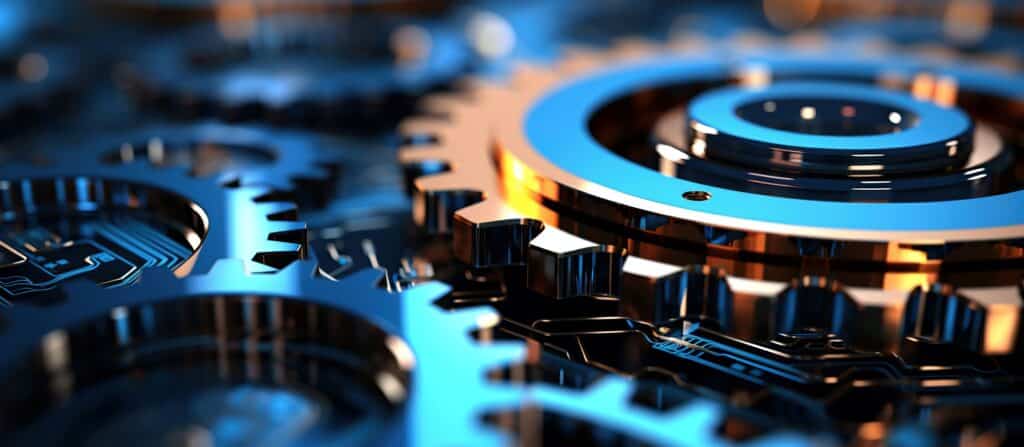
Spare parts are essential for the smooth running of a production plant, but at the same time, they are also a significant cost item. Therefore, effective management of spare parts inventory is crucial in any industrial environment. This minimizes production downtime, ensures continuous smooth operations, and effectively manages the value of inventory assets. To achieve this, it is worth focusing on defining and implementing analysis processes and continuous practices for stock management.
– Typical challenges in the manufacturing industry
– ABC analysis for inventory management
– A more comprehensive picture of inventory with two-dimensional analysis
– Actions based on the results of the analysis
Typical challenges in the manufacturing industry
In an industrial environment, effective management of spare parts inventory is a common challenge caused by several factors. Even in a medium-sized manufacturing plant, the spare parts inventory consists of thousands of different parts, each with its own characteristics, service life, order size, and process criticality level.
Without spare parts, it is impossible to keep production running smoothly. At the same time, these thousands of spare parts represent a significant investment for the factory. Additionally, the people responsible for warehouse operations often have their hands full with other daily activities, leaving very little time for development. Finding a balance in the spare parts inventory can also be challenging for industrial companies. Even though the worst COVID-related delivery time issues are starting to be behind us, there are still spare part categories where maintenance organizations must take risk mitigation activities by increasing the safety stock levels in the warehouse. Without a clearly defined, documented process, implementation plan, and annual schedule, warehouse-related development activities can easily be sidelined by other priorities and critical tasks at hand—leading to ever-increasing stock value, having obsolete items in stock, and increasing the workload of periodical inventory stocktaking due to the increased amount of stored items.
The good news is that effective inventory analysis and management is not rocket science. With appropriate analysis methods and targeted action planning, a framework for continuous improvement can be created, serving both the financial planning of the production facility and the reliability of production.
ABC analysis for inventory management
ABC analysis is a proven method used to cost efficiently allocate funds for spare parts for production, make better purchasing decisions and optimize order quantities. In ABC analysis, spare parts are classified into three categories based on their value:
A-items are the most important products in the inventory, representing approximately 70-80% of the total inventory value. These products typically account for about 10-20% of the items.
B-items are average products, representing approximately 15-25% of the total inventory value. These products typically account for about 30% of the items.
C-items are items that account for the remaining 5-10% of the total stock value, representing about 50-60% of the items.
A More Complete Picture of Your Inventory with Two-Dimensional Analysis
ABC analysis is an excellent starting point for improving awareness of spare part stock-related financial figures. However, using only ABC analysis can lead to decisions that compromise plant reliability. ABC analysis can also be conducted by measuring consumption value, calculated by multiplying the value of each spare part by its annual consumption. For two-dimensional analysis, it is better to use ABC classification based on the entire stock value.
Adding an additional dimension to the analysis can significantly improve the process and bring new aspects to decision-making. This additional analysis can be, for instance, combining stock value-based ABC analysis with Days of Supply (DOS) analysis. With a two-dimensional framework, you can get a more complete picture of your inventory, improve inventory optimization, secure plant reliability, reduce costs, and make better purchasing decisions.
Traditional ABC analysis focuses mainly on the value of an item, while DOS analysis tells you how many days of inventory are left based on annual consumption. This information helps you understand the demand patterns for inventory products and determine the appropriate reorder point, reorder quantity, and inventory level for each product.
Actions based on the results of the analysis
After a two-dimensional analysis, improvement actions can be more effectively targeted. For example, risk reduction can be achieved by ensuring the availability of items critical for the continuity of production, or activities can be targeted at lowering the total value of the warehouse across selected material categories. Even though spare parts in the A category tie up capital, as long as A-class items evidence continuous stock rotation, it typically indicates that their usage has valid reasons. When focusing on C items, an alternative procurement model can be considered to reduce costs.
The main focus should be on A category parts without continuous use. It is very common that the majority of these items don’t show any usage even in several years of stock takeout reports. This category should be reviewed by involving the right people who are familiar with each item to make informed decisions, especially if significant changes to safety stock levels or reorder quantities are made.
The number of items ending up in the A category can vary based on the industry segment and the size of the inventory. The easiest way to find the right balance for further analysis is by testing different percentages (70-80%) when determining the A-class scope.
Regular Analysis
Implementing actions and seeing results takes time and requires regular follow-up. After conducting the identified improvement measures, it is recommended to perform new analyses annually to see how the list of items has changed and how the total value has evolved. If there are noticeable changes in usage patterns, the first step is to adjust inventory levels. However, if the numbers are showing an unusual increase, it is advised to engage reliability maintenance methodologies to prevent unnecessary usage of parts.
By maintaining a proactive approach and regularly reviewing inventory practices, maintenance organizations can ensure optimal efficiency and cost-effectiveness, ultimately supporting sustained operational success.
If you are interested in learning more about how Quant can help your manufacturing operations, please don’t hesitate to contact us!