May 10, 2024
Condition-based maintenance – stop the firefighting and start predictive maintenance!
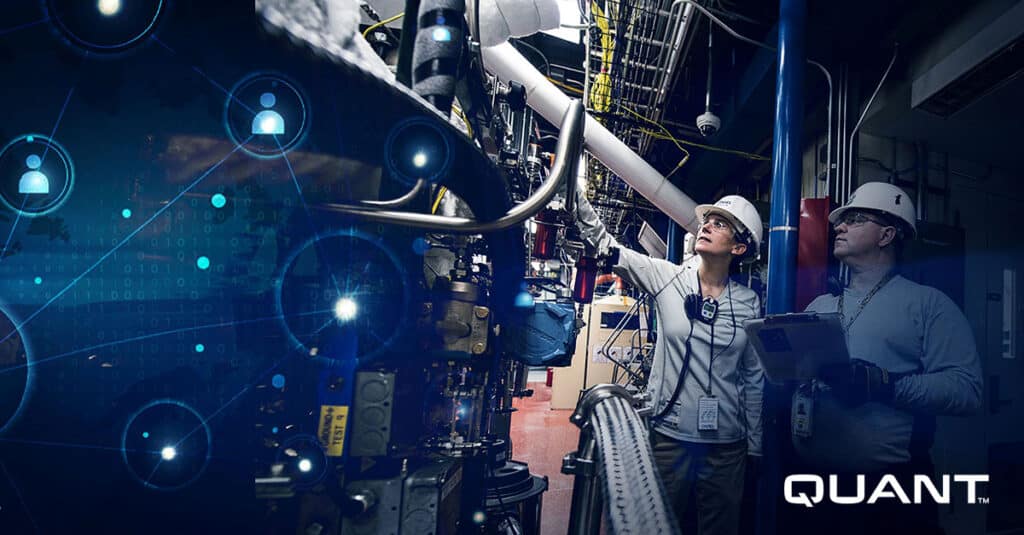
A higher production rate, a higher level of predictability, and lower costs with the possibility to optimize your maintenance intervals. All these highly valuable goals can be achieved by using condition-based maintenance processes to support your daily maintenance operations.
Nowadays, a lot of data is collected from different equipment and assets. How you use that data can make a difference. Reports or dashboards are ways to analyze or read the data, but that is not the whole story. The magic happens when maintenance operations are steered using accurate data of equipment condition.
Let’s take an example. Data might show that the bearing of a critical motor is starting to wear out. We have that data available weeks ahead of the point of failure. This means that the local maintenance unit, together with the production staff, can find the best possible time for the repair, plan it, schedule it, and execute as planned. No production loss, no additional damage, and it is the cheapest and quickest possible way to do the necessary repair.
All starts with condition monitoring
So what is needed to get started? It all starts with condition monitoring, which in practice means sensors on equipment in the production line collecting all the data. The raw data must be visualized and then analyzed. At Quant, we use our own cloud-based platform which can collect data from different suppliers’ sensors and give you an overview of multiple production lines from different manufacturers. The visualized data is analyzed by reliability engineers working proactively with the maintenance unit according to Quant’s reliability maintenance processes. In the end, the collected equipment condition data is turned to preventive maintenance actions.
What are the benefits shown in euros?
What is the benefits’ cost ratio? The easiest way is to show it using numbers. For example, for a mid-size mill, the yearly cost to run condition-based maintenance is between 15 000-20 000 euro. If the value of the production per line is 2000 euro/hour, the solution is beneficial if we can prevent as little as one eight hours long breakdown for one line per year! Other benefits, such as lower total maintenance cost, better production reliability, and ease of operations, are an added value that we can offer.
The collected data also enables optimized maintenance intervals. Almost every machine is maintained according to a monthly or yearly maintenance program. But very often, machines are running less than expected, although the maintenance is still done according to a stationary cycle. When operating data is available, maintenance intervals can be adjusted according to the actual operating time. This means fewer maintenance occasions, lower costs, and higher reliability by avoiding over-maintenance.
Are you interested in promoting a more planned maintenance approach? We have been developing our maintenance processes for over 35 years and we are happy to tell you more about the possibilities for how condition monitoring can be included in the operations of your production plant. Is it time to break free from firefighting, and run your plant with high reliability?
Lauri Kaiharju
Product Manager, Service Center, Quant Finland