October 3, 2024
Avoid unexpected maintenance costs
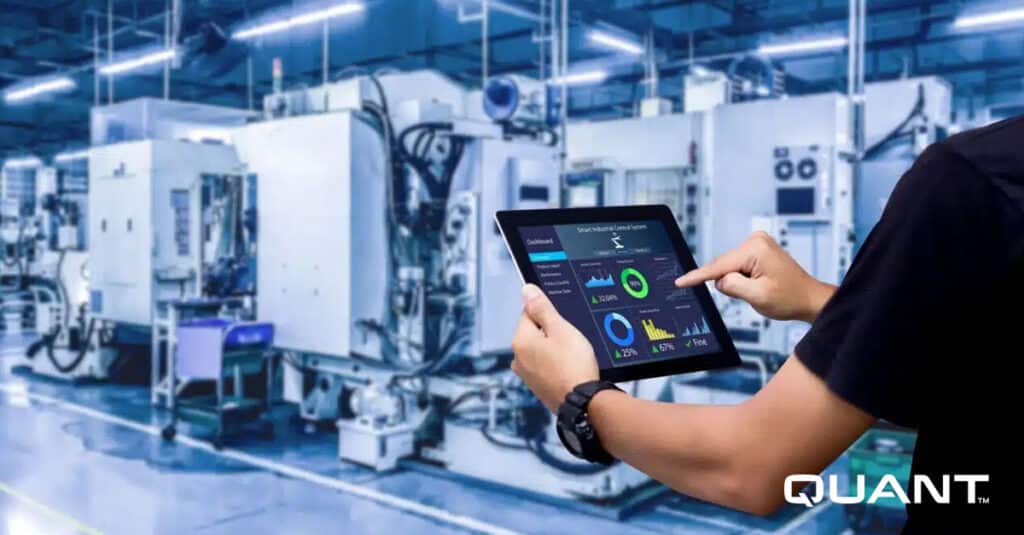
An unexpected production line shutdown can lead to significant production losses and high repair costs. In addition, it can result in decreased customer satisfaction, and even damage your reputation. Planned maintenance and proactive cost management are key to avoid such situations.
How can maintenance costs be predicted?
Operational and financial predictability go hand in hand. By basing operations on a long-term plan based on historical data, future costs can also be predicted. If predicting maintenance costs seems challenging, the development work should start with the maintenance management processes. Maintenance should have clear processes, operating models, and management.
Regarding historical data, a clear plan should also be formed for what data is collected, so that enough accurate information is available to support decisions. Trends formed by historical data enable the prediction of future costs and the making of controlled investment decisions. Historical data refers to information such as equipment repair costs, hours spent on repairs, and data collected through condition monitoring. For forecasting to be useful, data must also be monitored regularly.
Benefits of planned maintenance
Changing maintenance operations from reactive to planned brings significant benefits to the predictability of business operations.
From a budgeting perspective, maintenance planning enables the predictability of long-term costs. In addition, investment decisions can be made based on real facts. Predictability brings cost savings and improves operational management when preventive maintenance plans are based on equipment condition and costs are distributed more evenly. If operations are not planned, it often leads to large, unpredictable equipment failures that are very expensive. The situation is often reacted to in a hurry, which leads to additional costs and disruptions in production.
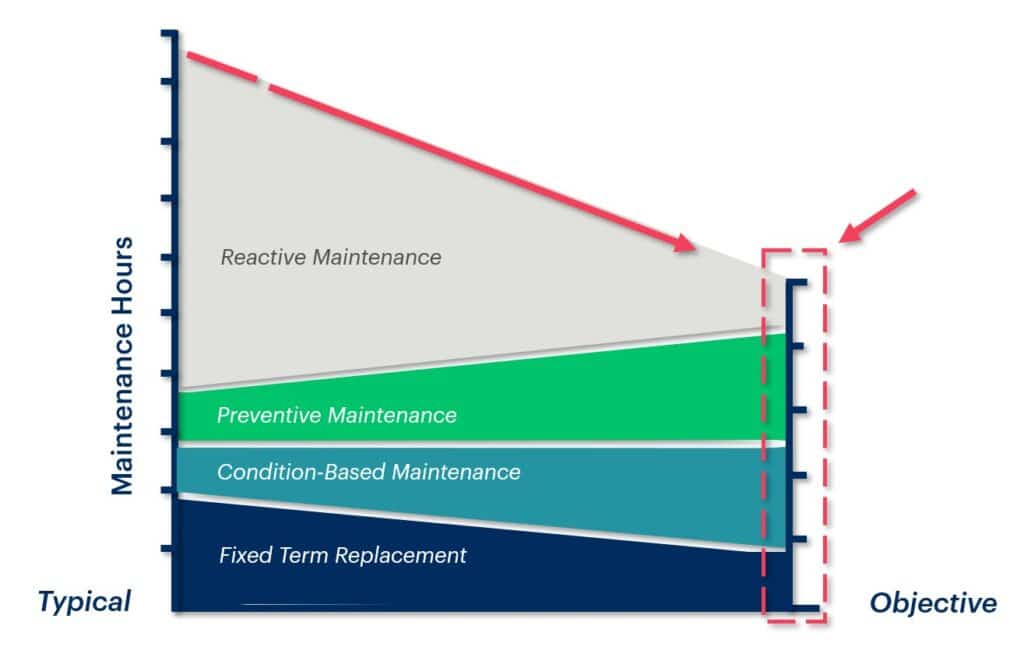
Planned maintenance enables resource planning based on real needs. Procurement and subcontracting resources are purchased according to a long-term plan, and overtime is carried out according to the resource needs of the preventive maintenance plan.
Reactive work and unplanned operations make risk management difficult. A long-term plan created based on historical data enables the creation of a budget, ensuring the right-timed resource needs, and minimizing unexpected production stops, unpredictable costs, and safety risks caused by unexpected equipment failures.
Planned maintenance enables operational efficiency and maximum production up-time when maintenance can be planned to be carried out at a time that suits the production. With the data collected by condition monitoring and the preventive maintenance plan, the resources in use can be utilized more efficiently.
Partner with Quant to optimize your maintenance and maximize your return
Our comprehensive maintenance solutions, based on industry-leading expertise and modern technology, deliver tangible results. With predictive analytics, we can predict equipment failures and plan maintenance proactively, minimizing downtime and reducing unexpected costs. A partnership with us can lead to:
- – Significant cost savings
- – Extended equipment lifetime
- – Improved productivity
- – Improved safety