March 20, 2025
Criticality Analysis for Optimizing Maintenance and Spare Part Strategies
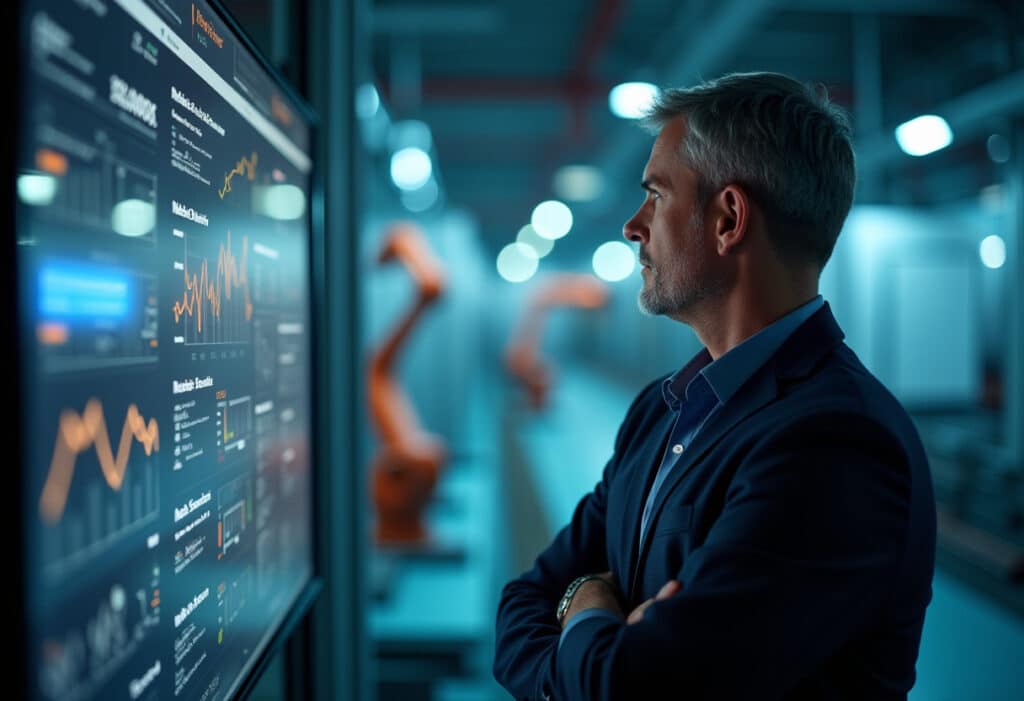
Understanding which machinery is most critical to operations can make a big difference in building efficient strategies for maintenance and bringing clarity to decision making. The classification process requires some effort and involvement from different stakeholders when categorizing machinery based on the impact of failure in terms of safety, environmental concerns, production, and cost. However, it is an effort worth taking since this analysis forms the basis for the subsequent enhancement of maintenance strategies, aiming to maximize resource efficiency and minimize downtime. In addition to the categorization of machinery, a management process is needed to ensure the criticality analysis remains dynamic and adaptable to changing plant conditions. This article outlines the methodology and results of a criticality analysis aimed at improving preventive maintenance plans and optimizing spare part management.
In any industrial environment, machinery failure can have significant consequences, including safety hazards, environmental damage, production delays, and increased costs. To mitigate these risks, companies must carefully prioritize their assets and allocate resources effectively. One of the most effective tools in achieving this goal is a Criticality Analysis, which helps to assess the relative importance of each piece of equipment. By evaluating the impact of machine failure across various domains, organizations can implement targeted strategies for maintenance and spare parts management.
Common Challenges in Implementing a Criticality Analysis
Despite its proven benefits, many organizations do not conduct or use criticality analysis to its full extent. There are several reasons for this. Firstly, the process may not be clear to all stakeholders, leading to confusion and inconsistent application. Secondly, there may be a lack of experience or use case examples to guide the implementation, making it difficult for teams to understand how to effectively apply the analysis. Additionally, criticality analysis can often be sidelined by other pressing activities and priorities, resulting in it being overlooked or not given the necessary attention. These challenges can prevent organizations from fully leveraging the potential of criticality analysis to optimize their inventory management and maintenance strategies.
Methodology: Conducting the Criticality Analysis
Carrying out a criticality analysis requires collaborative workshops involving representatives from both maintenance and production teams. The key steps in the analysis should be as follows:
Step 1: Identification of Equipment
Each machine in the operations should be catalogued. The focus should be on understanding the operational role of every asset, its criticality to the overall process, and how its failure would impact various aspects of the business.
Step 2: Evaluation Criteria
The analysis should be conducted using revised evaluation criteria to assess the potential consequences of failure across multiple dimensions. These criteria should comprehensively assess safety, environmental, production, and cost impacts, in addition to other key factors. It is always important to review these criteria before an analysis to ensure they align with the specific industry, size of the site, manufacturing process, and other relevant factors. Cost, for instance, can vary significantly depending on the industry branch.
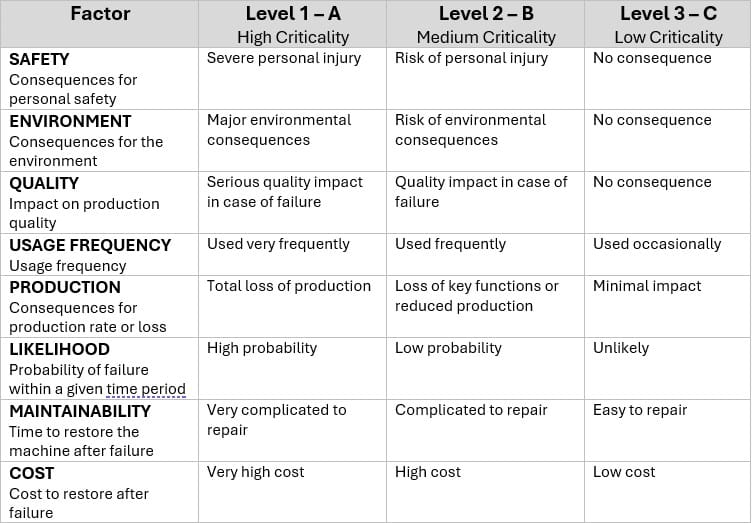
Step 3: Categorization of Machines
Once the machines are evaluated across these revised criteria, each machine should be categorized into one of three groups: A, B, or C. Additionally, a fourth category, E, could be used for machines that cannot be classified based on the provided criteria, such as workshop machines or non-production equipment.
Step 4: Results Documentation
Each machine should be assigned a category, and the results must be documented for use in future maintenance strategies. This categorization will directly influence the development of preventive maintenance schedules and spare parts strategies.
Developing a Management Process for Ongoing Criticality Analysis
Recognizing that a plant’s environment is dynamic and ever-changing, it is essential to develop a management process to ensure that the criticality analysis remains relevant and up-to-date. The following steps should be incorporated into the process:
Continuous Classification of New Machines: As new machinery is introduced to the plant, it is essential to classify it according to the same criteria used in the initial analysis. This ensures that the classification system reflects all operational assets and that new machines are properly prioritized within the maintenance and spare part strategies.
Reclassification of Existing Machines: Over time, the criticality of machines may change due to various factors, such as alterations in production processes, equipment upgrades, or failures that prompt root cause analysis. The management process should ensure that machinery is regularly reviewed and reclassified when necessary to reflect any significant changes in its impact on safety, the environment, production, or costs.
Root Cause Analysis and Adjustments: Following major breakdowns or incidents, a root cause analysis (RCA) should be conducted to determine whether the failure indicates a need for reclassification. For instance, if a Category B machine starts to cause significant production delays or safety concerns, it may need to be reclassified into Category A.
Monitoring and Continuous Improvement: The criticality analysis process should be monitored and periodically reviewed to ensure that it remains effective. Feedback loops from plant operators, maintenance teams, and other stakeholders should be used to improve the analysis and adjust processes as necessary.
The goal is to ensure that the plant’s asset management strategies are always aligned with the current operational context. This dynamic approach allows the company to adapt to changing needs, reduce downtime, and optimize resources.
Application to Preventive Maintenance and Spare Part Optimization
The results of the criticality analysis serve as the foundation for improving the company’s preventive maintenance and spare part optimization efforts. By understanding the relative importance of each machine, we can ensure that resources are used efficiently:
Preventive Maintenance (PM): Category A machines will be prioritized for more frequent inspections and maintenance activities, with advanced diagnostic tools and technologies employed to predict failures before they occur. Category B machines will be maintained according to a standard schedule, while Category C machines will have minimal preventive interventions, unless there is a specific risk identified.
Spare Part Optimization: Spare parts for Category A machines will be stocked and readily available, reducing downtime in the event of a failure. Category B machines will have spare parts on-hand but with longer replenishment times. For Category C machines, inventory levels will be kept to a minimum, ensuring cost savings without jeopardizing operation.
The implementation of these strategies will optimize resource allocation, improve the efficiency of maintenance operations, and reduce costs associated with downtime and spare part overstocking.
Summary – Why conduct a criticality analysis?
Criticality analysis is a powerful framework for optimizing maintenance and spare part strategies by prioritizing machinery based on various factors. This forms a robust approach for effective maintenance that maximizes resource efficiency and minimizes downtime. A dynamic management process ensures the analysis remains relevant and adaptable to changing plant conditions. If you are interested in how Quant can help you improve and optimize your maintenance processes and benefit your operations, please don’t hesitate to contact us!