July 2, 2025
Is your maintenance driving results – or just fixing failures?
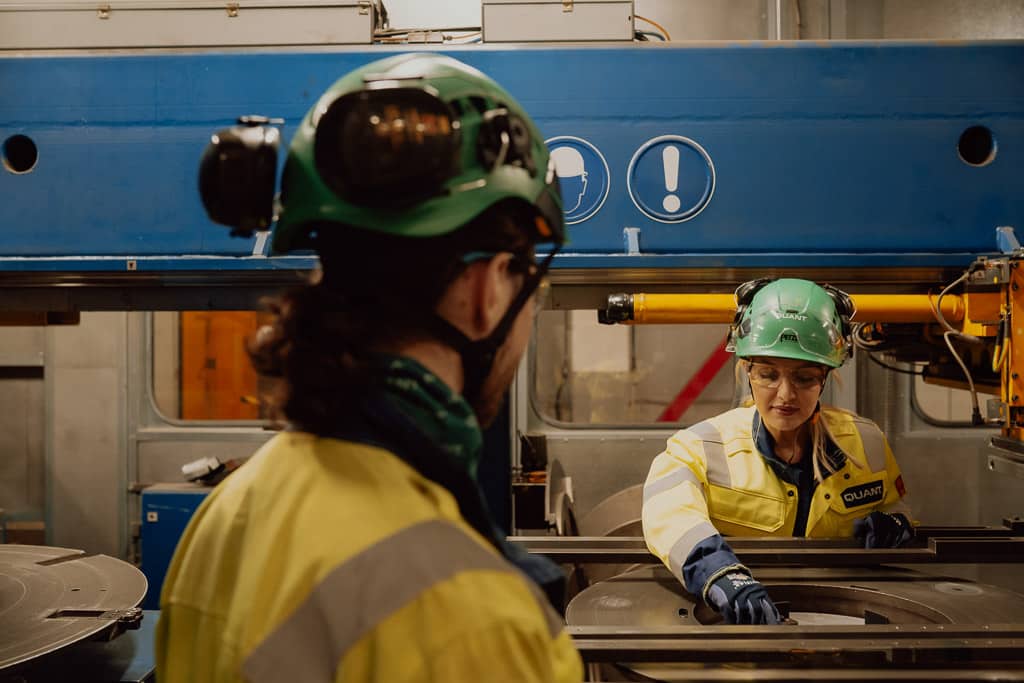
For many maintenance teams, reactive work is part of everyday life. Days are filled with urgent tasks, work backlogs grow longer, and overtime becomes the norm. Everyone knows that predictive maintenance could be the answer to constant firefighting, but few have a clear path forward, and planning often takes a back seat.
Predictive maintenance brings structure to daily operations: tasks can be scheduled, resourced, and prepared in advance. This frees up the team to focus on what truly matters, reduces pressure, and increases the sense of success at work.
“Everyone knows the difference between reacting and anticipating, but few manage to make it work in practice,” says Henri Chi, Sales Director at Quant Finland.
Quant’s customers have seen tangible improvements. The share of emergency work has dropped from 30% to 10%, backlogs have shortened from several weeks to just a few, and on-time task completion has significantly increased.
“We’ve developed an operational model that helps maintenance teams shift toward a more structured way of working step by step. At the core are clearly scheduled task management, resource planning, standardized tools, and continuous development supported by data,” Chi explains.
Our customers have experienced concrete benefits: resource needs are known in advance, overtime is reduced, spare part costs decrease, and equipment reliability improves. When equipment is maintained at the right time, its lifecycle is also extended.
How to move toward a more planned approach?
You don’t need to aim for 100% predictability. In certain cases, reactive work is part of a deliberate strategy. What matters most is building a maintenance process that supports your unit’s goals and enables continuous improvement.
“Change begins with measurement. When you understand how much of your maintenance is predictive versus reactive, you can set concrete targets. The optimal balance is well known in the industry: 70% predictive and 30% reactive,” Chi says.
Developing maintenance doesn’t happen overnight, but with the right solutions, progress is achievable. Reaching this goal requires systematic scheduling, resource management, task control, and effective communication.
“With Quant, predictive maintenance doesn’t stay on paper. Our model is based on step-by-step development, with full visibility along the way. We implement a practical framework that becomes part of your daily operations, with measurable results,” Chi emphasizes.
The goal is a working model that supports production, personnel, and strategic targets. If your maintenance still feels like constant reacting, now might be the right time to start the change.