May 6, 2024
From a cost center to a profit contributor – why invest in maintenance?
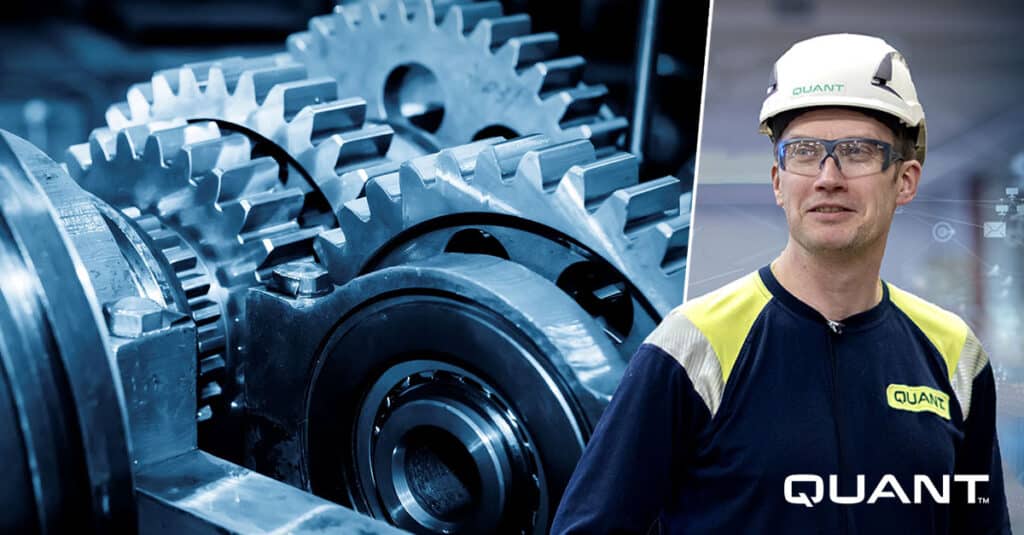
Even today, the maintenance function of an industrial facility is still often thought to be a cost factor among others. It is time to throw this thought model away. On the contrary, maintenance can decisively affect the productivity of the production facility and, with it, the result.
The effect of maintenance can most clearly be seen in the availability of production equipment, which is one component of overall equipment effectiveness, i.e. OEE, in addition to quality and speed. OEE should be one of the most important metrics in every production facility, and its development should be taken into account as part of the investment planning. When we talk about investments, we usually think of new equipment and technological innovations, which are aimed at increasing the factory’s capacity, driving speeds or, for example, improving quality. It would also be extremely important to think about how to maximize the availability and productivity of the devices throughout their life cycle. This means investing in maintenance as well. But how can investing in maintenance be justified?
An example of the benefits of investing in maintenance
Let’s go through it using a case. Let’s make a hypothesis about a factory with a production volume of 60,000 units per year and an annual turnover of 50 million euros. The selling price of one produced unit is therefore around 833 euros. The factory’s OEE is at the average level of the industry, about 67%. Product quality is fine, and production can be run at high speed. The challenges of this factory are related to availability, which is even below 80%.
For example, the low availability of the case factory is affected by frequently recurring device breakdowns and small technical malfunctions, which often take a long time to repair and recover from. Problems are only solved when they occur, and no time is set aside for their prevention and analysis or for the necessary development measures.
In this example, the investment would be aimed precisely at improving availability. Such an investment can include, for example, the reallocation of resources and time use, training, or the acquisition of additional resources and expertise combined with, for example, a new system solution.
In the case of this example factory, the focus would be on the systematic identification and elimination of events and disruptions that reduce usability, minimizing the loss of the factory’s operation and maintenance activities, and removing bottlenecks related to technical or operational processes by utilizing data and investing in additional resources focused specifically on usability challenges. It is important to note that achieving the goal often also requires a change in operating methods and processes.
The diagram below shows a scenario of the increase in production volume caused by the increase in OEE of an example factory, when availability is systematically improved over a four-year period by approximately 13% compared to the initial situation, while quality and speed remain unchanged:
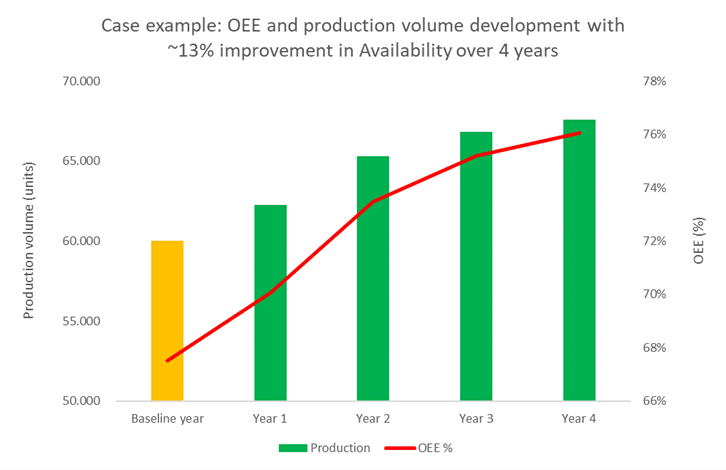
From this, we can derive the effect of increased production on revenue growth, assuming that all increased production can be sold and that the selling price remains constant:
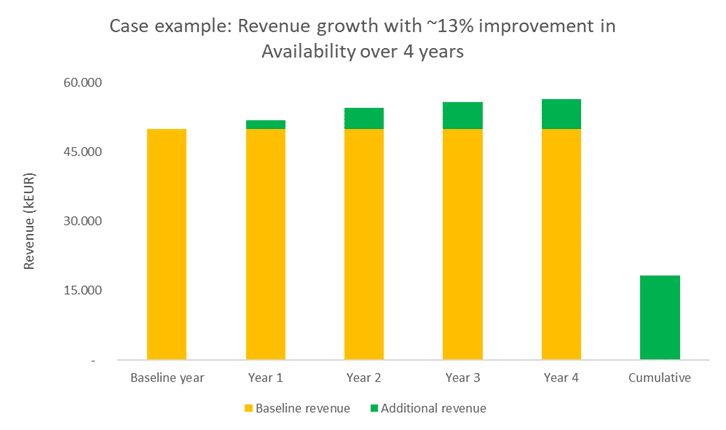
The cumulative revenue growth generated over four years can be up to around 18 million euros. With the help of the money received as an increased margin, we can calculate the payback period for the investment made in maintenance.
This example case is a simplified model that does not take into account all the legalities of the manufacturing business. However, it clearly explains why investing in maintenance is worthwhile.
Better productivity with a turnkey solution
Starting development projects is always easy but completing them, and especially maintaining permanent development processes, is significantly more difficult. Our Quant Site Operation Model offers clear processes and roles for managing different functions. Continuous improvement mechanisms are also built into the processes of our operating model, which improve the usability and production efficiency of our customers’ production facilities.
The implementation of Quant’s operating model offers a comprehensive turnkey solution to implement the above-described hypothesis in practice. We measure the performance of maintenance and production, utilize and analyze the collected data, identify causes and consequences with various tools and methods (such as root cause analyzes and failure, impact and criticality analyses) and implement a continuous improvement model to maximize the usability of the production plant, utilizing the experience we have acquired from various industries and the best practices we have collected.
Based on the above, our view at Quant is that maintenance is a profit contributor instead of a cost center.
Mikko Haanpää
Development Manager, Quant Finland