November 27, 2020
Develop your safety thinking
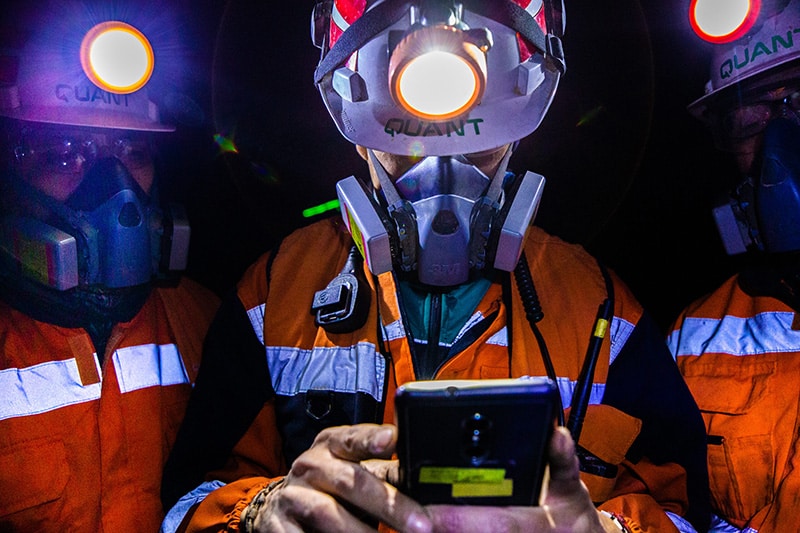
Have you ever come across a person at a workplace who says “if someone gets injured here, it’s just me” or “this is not dangerous, if you know what you’re doing”? Or even the more common comment “I have always done it this way and never had any accidents”? And the question is: How have you reacted to this?
The person in question would apparently be prepared to take responsibility for themselves, but is he or she also prepared to take responsibility for the safety of others present? Or does the person know that the supervisor is ultimately responsible for any accident, even if the employee consciously takes this risk? And most importantly: taking a conscious risk certainly violates both employer standards and occupational safety legislation.
Not everything always goes as planned. A carelessly assessed situation can also cause danger to others. Safe work, i.e. following instructions and regulations, taking care of the safety and health of other people working in the same working environment, taking care and immediately reporting hazards, deficiencies and faults, are the legal responsibilities of each worker. Taking care of safety is caring about oneself and one’s co-worker.
Sometimes you may come across the ill-advised thinking that there is no risk-taking if we are being aware of the risk while working. But the fact that we are aware of the risk but have not taken any corrective measures to reduce the risk, does not reduce the risk of an accident.
Over the years, positive developments in occupational safety thinking have taken the level of safety forward in many workplaces. Occupational safety has become an issue we want to invest in as a team. It’s only possible to succeed together, so everyone’s personal choice matters. Change starts with you.
Risk is a potential hazard that materializes when it comes into contact with for example a human being and an unexpected – or even easily observable – potential change factor. However, thinking that “this is how this has been done before” still lives on in some, but at the same time it is acknowledged that a less skilled and experienced technician would not be able to do it safely. At this point, all the internal alarm bells and sirens should go off in one’s head.
If everything always goes as before …
But what if it doesn’t? When assessing the probability of a risk and the severity of the consequences, we must understand that good luck cannot be relied upon. It is completely futile to assess the risks on the basis that the work will go just as planned. It is always possible that even the experienced and skilled technician makes a mistake, trips, falls, stumbles, loses consciousness, loses the grip on his tool, etc.
In fact, it is very likely that the technician with long experience will be the victim of a serious accident. This is evident from the statistics of the Finnish Accident Insurance Center – and this phenomenon has been seen in industrial accidents for decades.
In addition, any accident is often caused by several different factors or coincidences:
1. Something unexpected happens
– Something that the workers are not prepared for, even if the later investigation reveals that the event may have been very likely and has happened in the past.
2. Loss of control of the object, or machinery or part of machinery, and the work wasn’t prepared for it by using appropriate tools, guards, locks and brakes
– The tool slips or breaks down
– The machine part breaks or falls
– The machine or part of it moves, etc.
3. Due to some coincidence, the work is not done according to the original plan and the work pattern or method is changed
– It’s forgotten to carry out a new risk assessment, even though the nature of the work just changed, and thus the risks are different from what was originally assessed.
4. The working method is familiar and has been used for a long time
– At no point in the last years or decade has anyone questioned its safety or reasonability
All of the above are connected by one thing – the risk assessment. In connection with the identification of hazards, the reasons (the risks) leading up to the accident have not been successfully identified.
Why? Because there seems to be an invisible problem. There are dangerous or risky ways of working that have been used without a genuine understanding of their risks, and these ways of working do not come to light until something happens.
This approach, relying on professionalism and luck, is not sustainable in any workplace. Some day, the stars are in the wrong position, everything doesn’t go as planned, and all these potential dangers materialize … and someone gets injured, maybe seriously. It could be you. It could be your coworker.
So, stop, observe, question, and take into account the variables and plan, even if the job is already familiar to you from the past. Your choice to stop will ensure your safety as well as your co-worker’s.
Iiris Paavisto
Safety manager
Quant Finland