May 14, 2025
Predictive maintenance increases production output
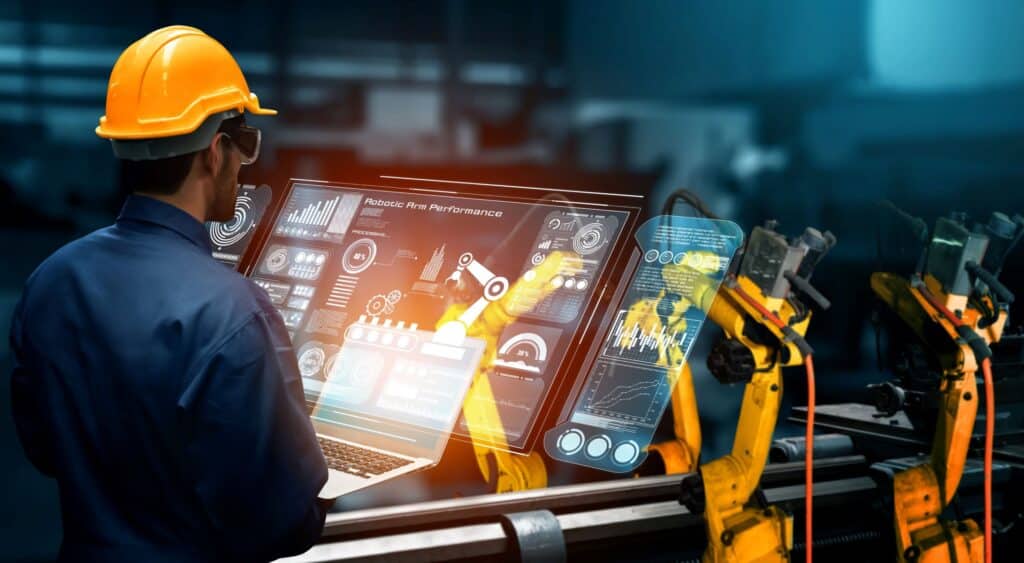
Depending on the industry, just one unplanned production stoppage can cost thousands of euros per hour. But what if it could be prevented? What if maintenance didn’t just react to problems, but actually steered production toward a more predictable, efficient, and safer direction?
In many industrial organizations, maintenance is still largely reactive. When something breaks, it’s fixed. But this often leads to a cycle of production interruptions, overtime, and additional costs.
What are the benefits of being proactive?
Predictive maintenance enables controlled production where issues are prevented before they occur. It brings predictability to operations, reduces overall costs, and extends the lifetime of equipment. When maintenance is seen as a strategic part of production, the added value it creates is significant.
While the idea of predictive maintenance is familiar to many, only a few production sites truly succeed in implementing it effectively. Quant’s customers have experienced clear benefits by shifting to a predictive approach. In one case, emergency work decreased from 30% to 10%, the work backlog was reduced from 7.5 weeks to 4.5 weeks, and the share of work completed on time increased to 90%. These improvements directly translated into increased productivity and bottom-line profitability.
“With predictive maintenance, resources are planned in advance – we know what will be done, when, and with what resources. Jobs are carefully prepared, and spare parts are ready at the right time. This reduces disruptions, minimizes downtime, and improves the utilization of production capacity,” says Lauri Kaiharju, Sales Manager, Quant Finland.
The impact is direct: higher production line efficiency and better business results. Predictive maintenance reduces production downtime, improves OEE, and brings consistency to operations. The capital tied up in spare part inventories decreases, overtime is reduced, and resources can be allocated more efficiently.
“When predictive maintenance is combined with the development of OEE (Overall Equipment Effectiveness), we can measure and optimize equipment availability, performance, and quality, all from a business-driven perspective,” Kaiharju adds.
“It’s a business decision”
Predictive maintenance is not just a technical solution, it’s a strategic business decision.
“It’s a business choice that enables better competitiveness and more profitable production. It helps avoid unexpected costs, ensures continuity in operations, and reduces environmental impact, for example by extending equipment lifecycles,” says Henri Chi, Sales Director, Quant Finland.
The industry has recognized an optimal balance for maintenance activities: 70% predictive and 30% reactive work. This ratio supports both cost efficiency and asset availability.
Striving for a 100% predictive model is rarely practical – for example, with machines nearing end-of-life, a reactive approach may still be the right choice.