januari 30, 2025
Digitala verktyg och underhållsanalys driver produktionstillväxt
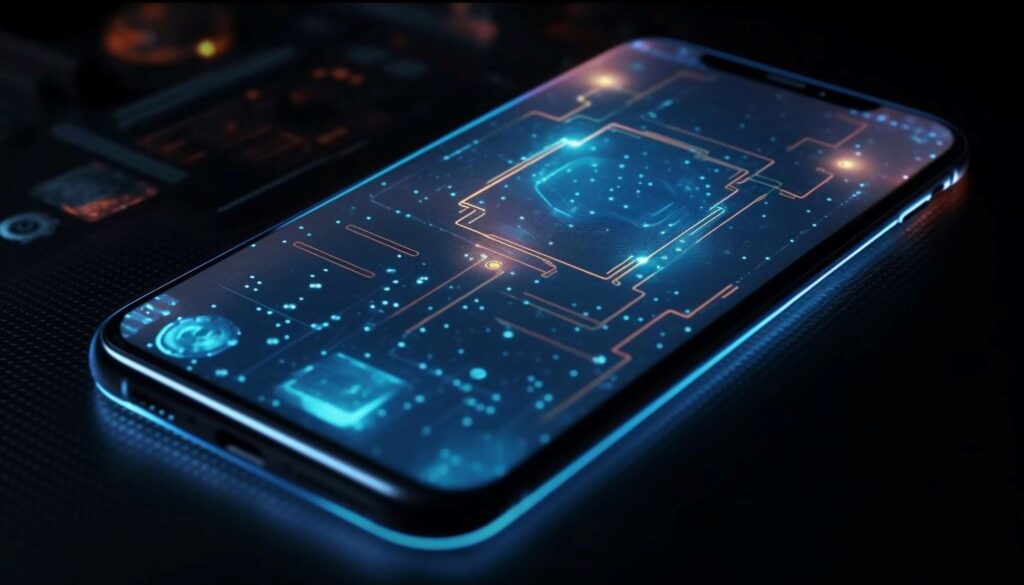
Tekniska framsteg driver förändring i flera branscher, vilket har lett till att integrationen av digitala verktyg och analys av data har blivit en nyckelfaktor för framgång. Inom underhåll har implementeringen av IoT-sensorer, artificiell intelligens (AI), maskininlärning (ML) och dataanalys drivit på utvecklingen i allt från tillverkningsindustrin till energisektorn. Dessa verktyg förhindrar inte bara driftstopp och förlänger utrustningens livslängd, utan minskar dessutom kostnader, förbättrar produktkvaliteten och ökar den totala effektiviteten. För industrier som strävar efter att förbli konkurrenskraftiga kan teknikens roll i att driva produktionstillväxt och främja hållbarhet inte överskattas.
Robert Berkel, Head of Digitalization & IT på Quant, har varit delaktig i flera projekt för att implementera moderna lösningar med målet att effektivisera underhållsprocessen.
”Tidigare har underhållsstrategier varit reaktiva, vilket innebär att underhållspersonalen agerar efter att felet redan har inträffat. Vårt mål är att nyttja digitala verktyg såsom IoT-sensorer och AI för att förutse och förhindra eventuella utrustningsfel”, säger Berkel.
Genom att utveckla en underhållsstrategi och nyttja moderna tekniska lösningar är det möjligt att förbättra produktionseffektiviteten för en anläggning med upp till 30 procent, beroende på utgångsläge och industri.
”Vi genomförde ett projekt hos vår kund där vi installerade IoT-sensorer på de mest kritiska enheterna, baserat på resultaten från en kriticitetsklassificering, och anslöt dem till ett molnbaserat system. Genom det lyckades vi minska tiden för oplanerade stopp med hela 144 timmar, bara på en anläggning”, säger Berkel.
IoT-sensorer och maskininlärning ökar produktionseffektiviteten och minskar kostnaderna
IoT-sensorer samlar in enhetsspecifika data om maskinens tillstånd, driftsförhållanden och prestanda i underhållssystemet, vilken analyseras för att implementera prediktiva underhållsåtgärder. Vanligtvis mäter IoT-sensorer exempelvis temperaturförändringar, vibrationsändringar, tryckskillnader, luftfuktighetsförändringar eller förändringar i strömförbrukning.
“Maskininlärning, en gren av artificiell intelligens, bygger på algoritmer. Det har revolutionerat det industriella underhållet under de senaste decennierna. Avancerade maskininlärningsalgoritmer förutsäger potentiella utrustningsfel baserat på insamlade data, vilket hjälper underhållsorganisationen att schemalägga planeradunderhåll, minimera produktionsstopp och optimera resursanvändningen”, säger Berkel.
De största fördelarna med att använda moderna tekniska lösningar för att förbättra underhållseffektiviteten uppnås vanligtvis inom områden där produktionsavbrott orsakar höga kostnader, såsom i tillverknings- och energisektorn.
Med hjälp av den information som görs tillgänglig genom digitala lösningar planerar underhållsorganisationen sitt arbete baserat på dataanalys och information som skapats av artificiell intelligens. Att utföra rätt underhåll vid rätt tid har en betydande inverkan på utrustningens livslängd, vilket möjliggör betydande kostnadsbesparingar och bättre schemaläggning av framtida investeringsbehov.
Dataanalys och visualisering gör beslutsfattandet snabbare
Vanliga användningsområden för visualiseringsskärmar är övervakning av utrustningens tillstånd, optimering av produktionsprocesser, övervakning av energiförbrukning samt lagerhantering. En visualiseringspanel kan till exempel visa realtidsmått, trenddiagram eller histogram.
Tillgänglig och lättläst information i realtid förbättrar och påskyndar beslutsfattandet. Förutsägbarheten bidrar till att minimera produktionsstopp och förlänger utrustningens livslängd, då underhåll kan utföras innan eventuella fel inträffar. Detta är ofta mer kostnadseffektivt, samtidigt som det är möjligt att öka produktionen och minska avfallet genom optimerade produktionsprocesser.
Förbättrad hållbarhet genom teknik
Förutom de operativa fördelarna ger integreringen av digitala lösningar även positiva effekter i hållbarhetsarbetet. Prediktivt underhåll minskar behovet av frekventa byten och reparationer, vilket minimerar avfall och sparar resurser. En energieffektiv verksamhet, som möjliggörs av övervakning och dataanalys i realtid, bidrar till att minska koldioxidavtrycket från industriell verksamhet. Genom att förlänga utrustningens livscykel och optimera resursutnyttjandet stöder dessa tekniker hållbara produktionsmetoder och bidrar till en grönare framtid.
Ökad säkerhet genom prediktivt underhåll
Att implementera tekniska lösningar i underhållsprocessen bidrar även till ökad säkerhet på arbetsplatsen. Genom att använda IoT-sensorer och maskininlärningsalgoritmer kan eventuella utrustningsfel förutsägas och åtgärdas innan de inträffar. Detta proaktiva tillvägagångssätt minimerar risken för olyckor och skador orsakade av oväntade utrustningshaverier. Dessutom gör övervakning och dataanalys i realtid det möjligt för underhållsorganisationen att snabbt identifiera och minska säkerhetsrisker, vilket bidrar till en säkrare arbetsmiljö för alla medarbetare. Implementeringen av dessa avancerade tekniker understryker vårt engagemang för att upprätthålla de högsta säkerhetsstandarderna samtidigt som vi optimerar produktionsprocesserna.