febrero 19, 2025
La tecnología moderna y los análisis de mantenimiento impulsan el crecimiento de la producción
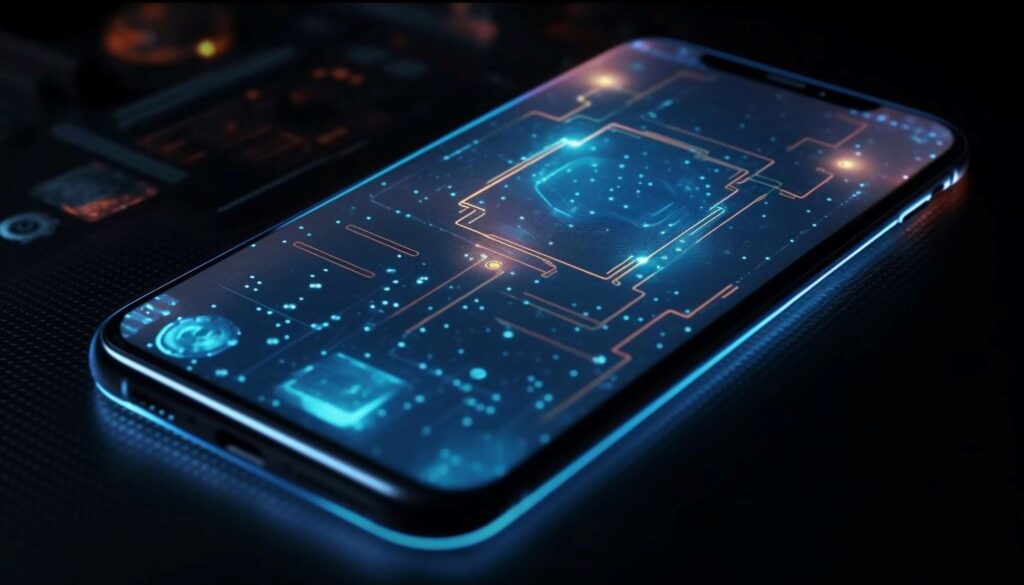
En una era en la que los avances tecnológicos están remodelando las industrias, la integración de herramientas y análisis de vanguardia se han convertido en la base principal para lograr la excelencia operativa. Desde el sector manufacturero hasta energético, la adopción de sensores de IoT, inteligencia artificial (IA), machine learning (ML) y análisis de datos están revolucionando las operaciones de mantenimiento. Estas tecnologías no sólo previenen el tiempo de inactividad y extienden los ciclos de vida de los equipos, sino que también reducen los costos, mejoran la calidad del producto y aumentan la eficiencia general. A medida que las industrias se esfuerzan por seguir siendo competitivas, no se puede subestimar el rol de estas innovaciones para impulsar el crecimiento de la producción y promover la sostenibilidad.
Robert Berkel, director de Digitalización y TI de Quant, ha estado implementando soluciones modernas para optimizar los procesos de mantenimiento industrial. “Por lo general, las estrategias de mantenimiento han sido reactivas, lo que significa que el personal de mantenimiento reacciona ante fallas de equipos que ya han ocurrido. Nuestro objetivo es aprovechar las herramientas tecnológicas, como los sensores de IoT y la IA, para prever y prevenir posibles fallos de los equipos”, afirma Berkel.
Al desarrollar una estrategia de mantenimiento y utilizar tecnología moderna, es posible mejorar la eficiencia de producción de una instalación hasta en un 30%, dependiendo de la situación inicial y el campo industrial. «Hemos implementado un proyecto en las instalaciones de nuestro cliente, instalando sensores IoT en los dispositivos más críticos según los resultados de la clasificación de criticidad y conectándolos a un sistema basado en la nube. Logramos reducir el tiempo de inactividad no planificado en 144 horas, en una sola planta», dice Berkel.
Los sensores de IoT y el aprendizaje automático aumentan la eficiencia de la producción y reducen los costos
Los sensores de IoT recopilan datos específicos del dispositivo sobre el estado, las condiciones operativas y el rendimiento de la máquina en el sistema de mantenimiento, que pueden analizarse para implementar medidas de mantenimiento predictivo. Normalmente, los sensores de IoT miden cambios de temperatura, cambios de vibración, diferencias de presión, cambios de humedad o cambios en el consumo de energía.
“Machine learning, una rama de la inteligencia artificial, se basa en algoritmos y ha revolucionado el mantenimiento industrial en las últimas décadas. Los algoritmos avanzados de aprendizaje automático predicen posibles fallos en los equipos a partir de los datos recopilados, lo que ayuda a la organización de mantenimiento a programar un mantenimiento proactivo, minimizar el tiempo de inactividad de la producción y optimizar la utilización de los recursos”, afirma Berkel.
Los mayores beneficios del uso de tecnología moderna para mejorar la eficiencia del mantenimiento generalmente se obtienen en campos donde las interrupciones de la producción causan costos excepcionalmente altos, como la fabricación y la energía.
Con la información obtenida a través de soluciones digitales, la organización de mantenimiento planifica el mantenimiento de los equipos mediante análisis de datos e información creada por inteligencia artificial. El mantenimiento en una etapa temprana tiene un impacto significativo en la vida útil del dispositivo, lo que permite ahorros sustanciales de costos y una mejor programación de las necesidades de inversión futuras.
El análisis y la visualización de datos agilizan la toma de decisiones
Los usos típicos de los paneles de visualización incluyen monitorear el estado del equipo, optimizar los procesos de producción, monitorear el consumo de energía y administrar el inventario. Por ejemplo, un panel de visualización puede mostrar métricas, gráficos de tendencias o histogramas en tiempo real.
La información en tiempo real, disponible y fácil de leer mejora y agiliza la toma de decisiones. La previsibilidad ayuda a minimizar el tiempo de inactividad de la producción y extiende el ciclo de vida de los equipos, ya que se puede reparar el equipo antes de que falle, lo que suele ser más rentable. Optimizando los procesos productivos es posible aumentar la producción y reducir los residuos.
Sostenibilidad a través de la tecnología
Además de los beneficios operativos, la integración de tecnología moderna en las prácticas de mantenimiento contribuye significativamente a los esfuerzos de sostenibilidad. El mantenimiento predictivo reduce la necesidad de reemplazos y reparaciones frecuentes, minimizando así el desperdicio y conservando recursos. Las operaciones energéticamente eficientes, habilitadas por el monitoreo y el análisis de datos en tiempo real, ayudan a reducir la huella de carbono de las actividades industriales. Al ampliar el ciclo de vida de los equipos y optimizar la utilización de recursos, estas tecnologías respaldan prácticas de producción sostenibles y contribuyen a un futuro más ecológico.
Mejora de la seguridad mediante el mantenimiento predictivo
La integración de tecnología moderna en las prácticas de mantenimiento no sólo aumenta la eficiencia operativa sino que también mejora significativamente la seguridad en el lugar de trabajo. Al utilizar sensores de IoT y algoritmos de aprendizaje automático, se pueden predecir y abordar posibles fallas de los equipos antes de que ocurran. Este enfoque proactivo minimiza el riesgo de accidentes y lesiones causados por averías inesperadas del equipo. Además, el monitoreo y el análisis de datos en tiempo real permiten a los equipos de mantenimiento identificar y mitigar los riesgos de seguridad rápidamente, garantizando un ambiente de trabajo más seguro para todos los empleados. La adopción de estas tecnologías avanzadas subraya nuestro compromiso de mantener los más altos estándares de seguridad y al mismo tiempo optimizar los procesos de producción.