junho 28, 2022
Increased efficiency and improved communication with quantWorxCode
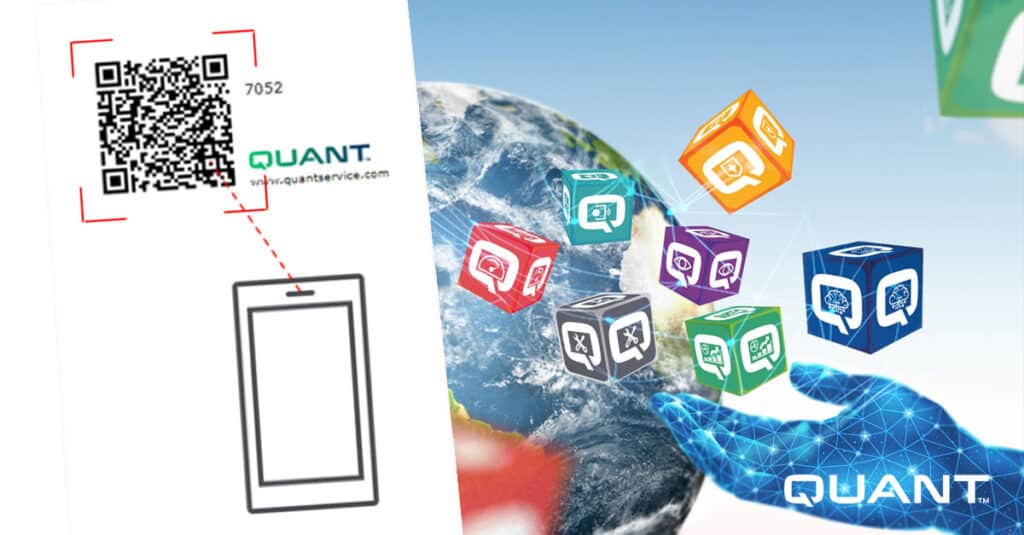
At one of our Finnish Quant sites, there is an ongoing project to implement the web-based application quantWorxCode. Using asset specific QR codes, the customer can create service requests, inspect ongoing work, or get in contact with the maintenance organization just by scanning the code with their smartphone.
At the end of 2021, a project to streamline the process of creating and handling work orders started at one of our sites in Finland when implementing quantWorxCode. Adding asset specific QR codes to the machines in the factory, the customer can scan these with their smartphone and create a service request, inspect ongoing work, or easily get in touch with the persons responsible for the maintenance of the machine.
– One of the main benefits is that we minimize the work orders received by email or phone, and instead get them directly into our CMMS system, says Quant Site Manager Henri Chi.
– There is always a risk that work orders get lost in someone’s email inbox or on a note on someone’s desk, but quantWorxCode makes this process very easy and efficient, both for the customer and for us.
Improved response time preventing larger machine failures
The application is completely web-based and does not require any pre-installation or signing in from the user. According to Henri, this is another key factor to why quantWorxCode has received very good feedback from the customer.
– From the customer’s point of view, they often have to communicate with a lot of different people and vendors, each of them proposing their own system with different usernames and passwords. But with quantWorxCode, having a smart phone is enough. So that is one of the problems we wanted to solve for the customer, making it as easy as possible for them, he says.
Another benefit for the customer is that the response time from the maintenance organization decreases, as streamlining the process has made it easier to report also small issues.
– The feedback received from the customer has been very positive. In plant environments, it is quite common that if a problem is not critical, it might not be immediately reported. So all of these small problems gather up, and it could take months until the maintenance organization is aware of them, Henri explains.
– By detecting these deviations early, we can decrease our response time and prevent larger failures.
Increased efficiency with quantWorxCode
The aim of the project is that all of the plant machines will be covered with asset specific QR codes at the end of the year, making the communication between the customer and the maintenance organization much more effective. But implementing quantWorxCode has also had a positive impact for the maintenance team and how they can plan and manage their work.
– In the short term, it increases the workload but in the long run, it will make our work a lot more efficient. Less investigation is needed, and we have the information directly in our CMMS system which allows us to be more effective and proactive, Henri says.